Silicon MEMS piezoresistance type acceleration sensor
An acceleration sensor and piezoresistive technology, applied in the field of micromechanical sensors, can solve the problems of increasing processing difficulty and reducing sensor accuracy, and achieve the effects of easy three-axis integration, light weight, and reducing processing difficulty
- Summary
- Abstract
- Description
- Claims
- Application Information
AI Technical Summary
Problems solved by technology
Method used
Image
Examples
Embodiment 1
[0017] like figure 1 shown. The silicon MEMS piezoresistive acceleration sensor of the present embodiment is to arrange a quality block 2, two torsion beams 3 and four sensitive beams 4 in a silicon frame 1, and the mass block 2 is positioned at the middle of the silicon frame 1, and passes through the torsion beam 3. The sensitive beam 4 is connected to the silicon frame 1; the sensitive beam 4 is symmetrically distributed on the left and right sides of the mass block 2, and the torsion beam 3 is located on the front and rear sides of the mass block 2; the height of the sensitive beam 4 in the vertical direction and the width in the horizontal direction Far smaller than the height and width of the mass block 2; the torsion beam 3 is located on the centerline of the planes on both sides of the mass block 2, the height of the torsion beam 3 in the up and down direction is the same as that of the mass block 2, and the width in the horizontal direction is smaller than that of the...
Embodiment 2
[0019] like figure 2 shown. The difference between this embodiment and Embodiment 1 is that there is one sensitive beam 4 on the left and right sides of the mass block 2, and the two sensitive beams 4 are symmetrically distributed on the center line of the left and right planes of the mass block 2. A piezoresistor 5 is arranged at both ends of the beam 4 respectively, and four piezoresistors can form a measuring bridge. A pair of torsion beams 3 are arranged on the front-to-back centerline of the mass block, the vertical height of which is greater than the vertical height of the sensitive beam 4 and smaller than the vertical height of the mass block 2 .
Embodiment 3
[0021] The difference between this embodiment and Embodiment 1 is that a piezoresistor 4 is respectively arranged at both ends of each sensitive beam 4, and there are 8 piezoresistors on the four sensitive beams, which can form two measurement circuits. bridge.
PUM
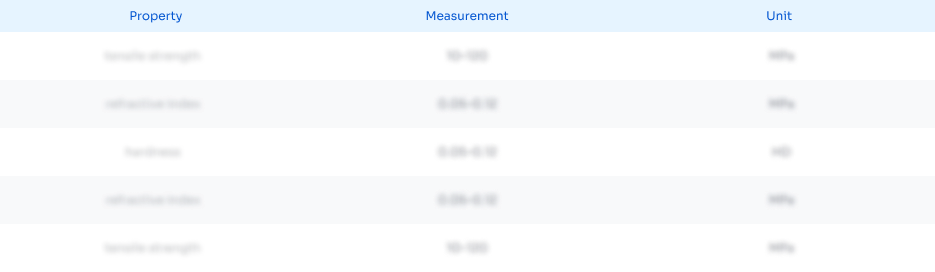
Abstract
Description
Claims
Application Information

- R&D
- Intellectual Property
- Life Sciences
- Materials
- Tech Scout
- Unparalleled Data Quality
- Higher Quality Content
- 60% Fewer Hallucinations
Browse by: Latest US Patents, China's latest patents, Technical Efficacy Thesaurus, Application Domain, Technology Topic, Popular Technical Reports.
© 2025 PatSnap. All rights reserved.Legal|Privacy policy|Modern Slavery Act Transparency Statement|Sitemap|About US| Contact US: help@patsnap.com