Method for manufacturing dimethyl ether with solid acid catalysis methanol dehydration reaction
A technology of solid acid catalysis and solid acid catalyst, which is applied in the dehydration of hydroxyl-containing compounds to prepare ethers, chemical instruments and methods, molecular sieve catalysts, etc. It can solve uneven temperature distribution, difficult large-scale chemical industrial production, and difficult catalyst bed temperature, etc. question
- Summary
- Abstract
- Description
- Claims
- Application Information
AI Technical Summary
Problems solved by technology
Method used
Examples
Embodiment 1
[0028] Embodiment 1: Dehydration of fixed-bed methanol to produce dimethyl ether
[0029] Catalyst is the same as Comparative Example 1. 2500 milliliters of catalyst was loaded into a fixed-bed reactor with an inner diameter of 37 mm, and there were four injection points of chilled materials along the axial direction of the catalyst bed section of the reactor. Temperature is 125 ℃ of liquid methanol (purity is 97.5% (weight)) at space velocity 0.102 hours -1 Evenly injected into the reactor.
[0030] At a reactor inlet temperature of 210°C, a reaction pressure (gauge pressure) of 1.1MPa, and a methanol feed space velocity of 3 hours -1 Under the above conditions, the conversion rate of methanol is 75.1%, the selectivity of dimethyl ether is ~100%, the outlet temperature of the bed is 220°C, the highest temperature point of the bed is 225.1°C, and the average temperature of the bed is 215.6.
Embodiment 2
[0031] Embodiment 2: Dehydration of fixed-bed methanol to produce dimethyl ether
[0032] Catalyst, reactor, methanol raw material, quenching material are the same as embodiment 1.
[0033] At a reactor inlet temperature of 225°C, a reaction pressure (gauge pressure) of 1.1MPa, and a methanol feed space velocity of 3 hours -1Under the above conditions, the conversion rate of methanol is 86.2%, the selectivity of dimethyl ether is 99.99%, the outlet temperature of the bed is 237°C, the highest temperature point of the bed is 241.0°C, and the average temperature of the bed is 232.2°C.
Embodiment 3
[0037] Embodiment 3: Dehydration of fixed-bed methanol to produce dimethyl ether
[0038] Catalyst, reactor and methanol raw material are the same as Comparative Example 3.
[0039] At a reactor inlet temperature of 140°C, a reaction pressure (gauge pressure) of 1.0 MPa, and a methanol feed space velocity of 2.0 hours -1 Under the above conditions, the conversion rate of methanol is 66.1%, the selectivity of dimethyl ether is ~100%, the outlet temperature of the bed is 145.0°C, the highest temperature point of the bed is 150.2°C, and the average temperature of the bed is 142.1°C.
PUM
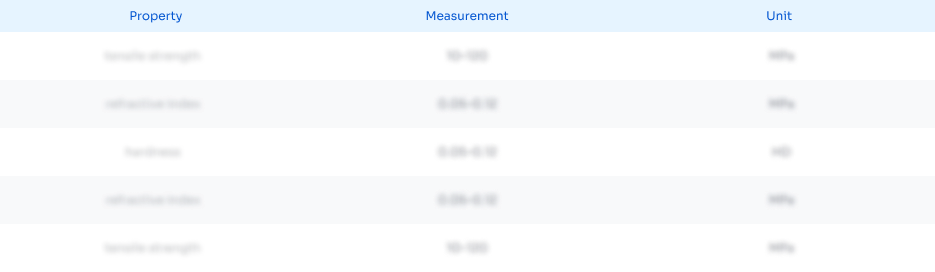
Abstract
Description
Claims
Application Information

- R&D Engineer
- R&D Manager
- IP Professional
- Industry Leading Data Capabilities
- Powerful AI technology
- Patent DNA Extraction
Browse by: Latest US Patents, China's latest patents, Technical Efficacy Thesaurus, Application Domain, Technology Topic, Popular Technical Reports.
© 2024 PatSnap. All rights reserved.Legal|Privacy policy|Modern Slavery Act Transparency Statement|Sitemap|About US| Contact US: help@patsnap.com