Wood bunch recombining material and producing method thereof
A technology for reconstituting wood and wood bundles, which is applied in the direction of wood processing appliances, other household appliances, pretreatment of molding materials, etc. The secondary processing into wood products is easy, the technical requirements and investment are low, and the effect of eliminating wood growth stress
- Summary
- Abstract
- Description
- Claims
- Application Information
AI Technical Summary
Problems solved by technology
Method used
Examples
Embodiment 1
[0016] Embodiment 1: collect poplar branches, after removing impurities such as bark and silt, send into timber longitudinal rolling strip cutting machine, make wood beam strip, dry to moisture content 8-12%, spray phenolic resin glue, The sizing amount of the thicker and longer is 4%, and the sizing amount of the shorter and thinner is 5%. After a little drying, the thick, thin, long and short wood strips are evenly mixed and measured. After directional paving, they are directly moved into the mold for cold pressing, and the pressure is 7MPa. , pressurized for 3-5 minutes, fixed and sent to the drying room together with the mold after molding, gradually heated from room temperature to 140 ° C, cured for 18 hours, after curing, moved outdoors together with the mold to cool naturally to room temperature, and the density was about 0.9 after demoulding. g / cm 3 of recombined wood.
Embodiment 2
[0017] Embodiment 2: Gather thinning small-diameter Chinese fir and processed Chinese fir corner waste, send it to the longitudinal rolling and cutting machine for wood, make wood beam strips, dry to about 10% moisture content, and dip phenolic resin glue in two batches, The amount of sizing is controlled by the length of immersion time, and after draining, it is dried again to a moisture content of 10-16%, and after mixing, it is measured, oriented, bundled, and molded. The cold pressing pressure is 5MPa, and the pressing time is 3-5min. Same as Example 1, the obtained density is about 0.7g / cm 3 fir reconstituted wood.
[0018] The column of recombined wood obtained by the method can be directly used as a column for the building decoration industry, or can be sawed and cut to make floors, furniture panels and the like.
PUM
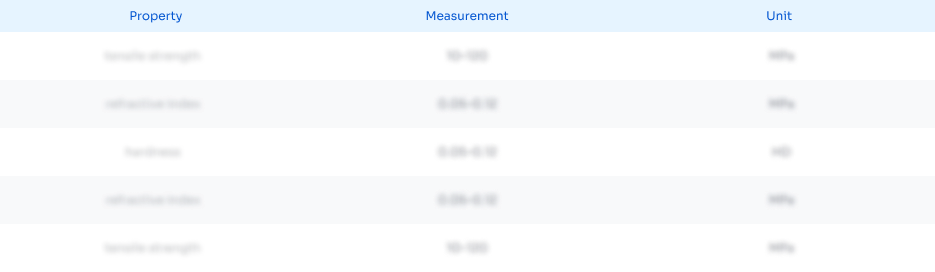
Abstract
Description
Claims
Application Information

- R&D
- Intellectual Property
- Life Sciences
- Materials
- Tech Scout
- Unparalleled Data Quality
- Higher Quality Content
- 60% Fewer Hallucinations
Browse by: Latest US Patents, China's latest patents, Technical Efficacy Thesaurus, Application Domain, Technology Topic, Popular Technical Reports.
© 2025 PatSnap. All rights reserved.Legal|Privacy policy|Modern Slavery Act Transparency Statement|Sitemap|About US| Contact US: help@patsnap.com