Hot rolled wire material excellent in cold forging property after spheroidizing treatment, spheroidizing-annealed steel wire having excellent cold forging property, and method for production thereof
A technology of spheroidizing annealing and manufacturing method, which is applied to hot-rolled wire rods with excellent cold forgeability after spheroidizing treatment, spheroidizing annealed steel wires with excellent cold forgeability, and their manufacturing fields, and can solve the problem of cold working. Deformation resistance becomes higher, cementite processing performance is reduced, tool life is reduced, etc., to reduce deformation resistance, hardenability and cold forging strength, and achieve the effect of processing performance.
- Summary
- Abstract
- Description
- Claims
- Application Information
AI Technical Summary
Problems solved by technology
Method used
Image
Examples
Embodiment 1
[0127]Steels with the compositions shown in Table 1 were subjected to wire rolling (hot rolling) under the conditions of cooling rates and constant temperature holding times in Tables 2 to 4 to produce hot-rolled steels having the structures shown in Tables 2 to 4. wire. In Table 1, steels A to E are within the scope of the invention of the present application, steel F is a sample with higher Cr and N than the range of the present application, and steel G is a sample with high Cr.
[0128] Ceq (carbon equivalent) in Tables 1 and 2 is Ceq=C%+(1 / 3)Si%+(1 / 6)Mn%. Here, C%, Si%, and Mn% in the formula represent the contents (mass %) of C, Si, and Mn in the hot-rolled wire rod, respectively.
[0129] The hot-rolled wire rod in A c1 Quickly perform spheroidizing annealing directly below the point (heating to A at a rate of 150°C / hour c1 Point directly below, at A c1 point directly below for 1 hour before air cooling).
[0130] Using a test piece (ratio of cylinder height h to di...
Embodiment 2
[0152] Steels having steel components I to V shown in Table 5 were hot-rolled under the following conditions to produce hot-rolled wire rods. After rolling, the steel is coiled at 750-1000°C. Next, cool from the upper limit temperature of 750 to 1000°C to the lower limit temperature of 400 to 550°C at a cooling rate of 20 to 100°C / sec, and keep at the constant temperature holding temperature shown in Table 6 for more than 20 seconds to complete Isothermal phase transformation, cooling to room temperature, to obtain hot-rolled wire rod.
[0153] Then, the hot-rolled wire rod is rough-drawn with the area reduction rate shown in Table 6, and spheroidized annealed (heating at a speed of 150° C. / hour to A 1 point directly below point A1, keep it for 1 hour directly below point A1, then carry out air-air cooling), and then perform fine wire drawing at the area reduction rate shown in Table 6.
[0154] table 5
[0155]
steel
Steel composition (mass%)
...
PUM
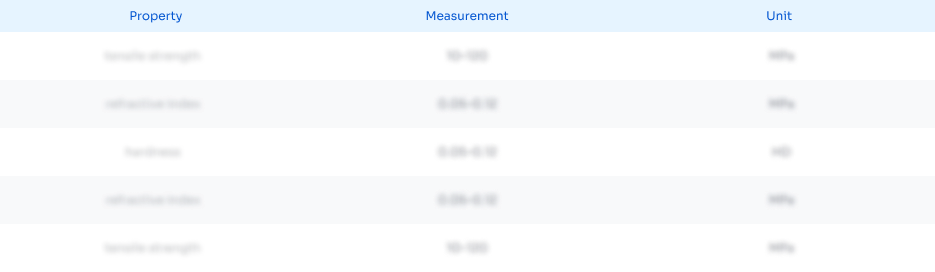
Abstract
Description
Claims
Application Information

- R&D Engineer
- R&D Manager
- IP Professional
- Industry Leading Data Capabilities
- Powerful AI technology
- Patent DNA Extraction
Browse by: Latest US Patents, China's latest patents, Technical Efficacy Thesaurus, Application Domain, Technology Topic, Popular Technical Reports.
© 2024 PatSnap. All rights reserved.Legal|Privacy policy|Modern Slavery Act Transparency Statement|Sitemap|About US| Contact US: help@patsnap.com