Temperature-resistant resin modified polyphenyl ester ternary alloy ultrasonic motor friction material
A technology of high temperature resistant resin and ternary alloy, applied in the field of polyphenylester composite materials, can solve the problems of small friction coefficient, unsatisfactory wear resistance, poor processing performance, etc., and achieve the effect of superior thermal stability
- Summary
- Abstract
- Description
- Claims
- Application Information
AI Technical Summary
Problems solved by technology
Method used
Image
Examples
specific Embodiment approach 1
[0005] Specific embodiment one: In this embodiment, the high temperature resistant resin modified polyphenyl ester ternary alloy ultrasonic motor friction material is made of polytetrafluoroethylene, high temperature resistant resin and polyphenyl ester, wherein polytetrafluoroethylene accounts for 5% of the total weight ~25%, the high temperature resistant resin accounts for 5~20% of the total weight, and the rest is polyphenylene.
specific Embodiment approach 2
[0006] Embodiment 2: In this embodiment, polytetrafluoroethylene accounts for 7-15% of the total weight, high-temperature-resistant resin accounts for 7-15% of the total weight, and the rest is polyphenylene ester. Others are the same as in the first embodiment.
specific Embodiment approach 3
[0007] Embodiment 3: In this embodiment, polytetrafluoroethylene accounts for 10% of the total weight, high temperature resistant resin accounts for 10% of the total weight, and polyphenylene accounts for 80% of the total weight. Others are the same as in the first embodiment.
PUM
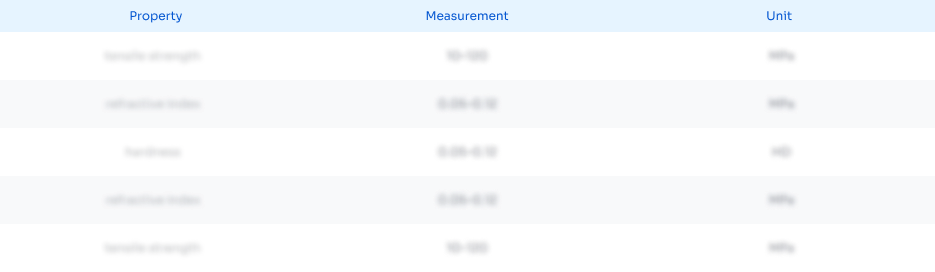
Abstract
Description
Claims
Application Information

- R&D
- Intellectual Property
- Life Sciences
- Materials
- Tech Scout
- Unparalleled Data Quality
- Higher Quality Content
- 60% Fewer Hallucinations
Browse by: Latest US Patents, China's latest patents, Technical Efficacy Thesaurus, Application Domain, Technology Topic, Popular Technical Reports.
© 2025 PatSnap. All rights reserved.Legal|Privacy policy|Modern Slavery Act Transparency Statement|Sitemap|About US| Contact US: help@patsnap.com