Vanadium catalysis system for combined polymerization of ethylene, propylene, and diolefin, and application
A catalytic system and diene technology, applied in the field of vanadium catalytic system, can solve the problems of difficulty in post-processing of rubber, secondary pollution of polymers, insufficient activity, etc., and achieve lower production catalyst cost, improved ternary copolymerization activity, and easy removal. Effect
- Summary
- Abstract
- Description
- Claims
- Application Information
AI Technical Summary
Problems solved by technology
Method used
Examples
Embodiment 1
[0036] Prepare ethylene, propylene, and hydrogen through a mixing device according to 1: (1.5-4.5): (0.15-0.45), and then fully mix them evenly through a circulating compressor. The polymerization is carried out in a 5L polymerization kettle, and the 5L polymerization kettle Perform anhydrous and oxygen-free treatment under vacuum for 1 hour, the inert gas used is high-purity nitrogen, then add 2000ml of dry hexane (water content≤10ppm) to it, which contains 10ml of norbornene (ENB), and start the cycle compression machine, feed the mixed gas into the polymerization kettle to make the mixed gas dissolved in hexane reach saturation, and then add 10ml (0.4mmol) of bis (diisooctyl phosphate) vanadyl (V-P 204 ) of hexane solution, 10ml of sesquialuminum, so that the Al / V ratio is 20 / 1, and finally add activator ethyl trichloroacetate (ETCA), so that ETCA / V is 5 / 1, and the polymerization temperature is 30°C. The pressure is 0.5MPa, and the polymerization reaction time is 1 hour. Af...
Embodiment 2
[0038] Change the add-on of ethyl trichloroacetate (ETCA), make ETCA / V be 3 / 1, other conditions are identical with embodiment 1, make Al / V ratio be 10 / 1, get dry glue 118g, polymerization catalytic efficiency 5784g glue / g vanadium. Through gel permeation chromatography analysis, the number average relative molecular mass is 40,000, the relative molecular mass distribution is 2.7, and the propylene content is 40%.
Embodiment 3
[0040] Other conditions are identical with embodiment 1, change the add-on of ethyl trichloroacetate (ETCA), make ETCA / V be 8 / 1, make Al / V ratio be 40 / 1, get dry glue 120g, polymerization catalytic efficiency 5882g glue / g vanadium. Through gel permeation chromatography analysis, the number average relative molecular mass is 31,000, the relative molecular mass distribution is 3.0, and the propylene content is 39%.
PUM
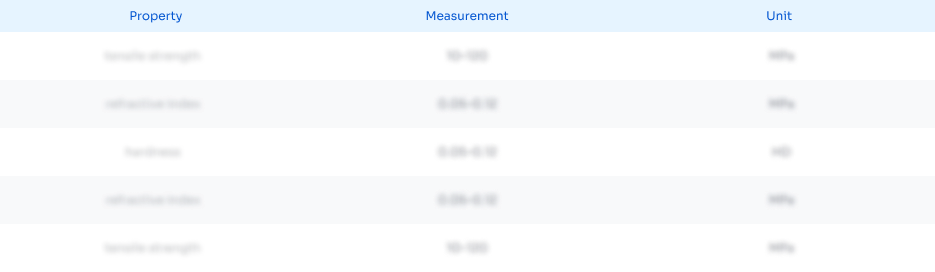
Abstract
Description
Claims
Application Information

- Generate Ideas
- Intellectual Property
- Life Sciences
- Materials
- Tech Scout
- Unparalleled Data Quality
- Higher Quality Content
- 60% Fewer Hallucinations
Browse by: Latest US Patents, China's latest patents, Technical Efficacy Thesaurus, Application Domain, Technology Topic, Popular Technical Reports.
© 2025 PatSnap. All rights reserved.Legal|Privacy policy|Modern Slavery Act Transparency Statement|Sitemap|About US| Contact US: help@patsnap.com