Antibacterial polypropylene material and its prepn process
A technology of antibacterial polypropylene and polypropylene resin, which is applied in botany equipment and methods, biocides, plant growth regulators, etc., can solve the problems of unsustainable, poor antibacterial performance, and high production costs, and achieve reduced production costs and weather resistance Performance improvement, rapid effect of antibacterial performance
- Summary
- Abstract
- Description
- Claims
- Application Information
AI Technical Summary
Problems solved by technology
Method used
Image
Examples
preparation example Construction
[0034] Please refer to Fig. 1, prepare the preparation method of described antibacterial polypropylene material, comprise the following steps:
[0035] Step 1: Weigh 100 parts of polypropylene resin, 25 to 35 parts of filler, 5 to 15 parts of toughening agent, 0.2 to 0.8 parts of antibacterial agent, 0.5 to 1.5 parts of dispersant, and 0.1 to 0.5 parts of antioxidant according to weight ratio parts, 0.1 to 0.5 parts of ultraviolet absorbers;
[0036] Step 2: Mix the components weighed in step 1 in a high-speed mixer for 3 to 5 minutes;
[0037] Step 3: Place the mixed components in a parallel twin-screw extruder for melt extrusion and granulation.
[0038] The extrusion process of the parallel twin-screw extruder is: 1 zone 170--180 ℃, 2 zone 180--190 ℃, 3 zone 180-190 ℃, 4 zone 175-185 ℃, screw speed 300-350r / min, feeding frequency 15~20Hz, melt pressure 3.0~4.0MPa, vacuum degree -0.03--0.06Mpa.
Embodiment 1
[0042] In parts by weight, mix 100 parts of PP resin, 25 parts of filler, 5 parts of toughening agent, 0.2 part of antibacterial agent, 0.5 part of dispersant, 0.1 part of antioxidant, and 0.1 part of ultraviolet absorber in a high-speed mixer 3 to 5 minutes, the speed of the high-speed mixer is 800 rpm; then the mixed raw materials are placed in a parallel twin-screw extruder for melt extrusion and granulation. The extrusion process is: 1 zone 170--180 ℃ , Zone 2 180--190°C, Zone 3 180--190°C, Zone 4 175--185°C, screw speed 300-350r / min, feeding frequency 15-20Hz, melt pressure 3.0-4.0MPa, vacuum degree -0.03---0.06MPa.
Embodiment 2
[0044] In parts by weight, 100 parts of PP resin, 30 parts of filler, 10 parts of toughening agent, 0.5 part of antibacterial agent, 1 part of dispersant, 0.3 part of antioxidant, 0.3 part of ultraviolet absorber, mixed in a high-speed mixer 3 to 5 minutes, the speed of the high-speed mixer is 800 rpm; then the mixed raw materials are placed in a parallel twin-screw extruder for melt extrusion and granulation. The extrusion process is: 1 zone 170--180 ℃ , Zone 2 180--190°C, Zone 3 180--190°C, Zone 4 175--185°C, screw speed 300-350r / min, feeding frequency 15-20Hz, melt pressure 3.0-4.0MPa, vacuum degree -0.03-- -0.06MPa.
PUM
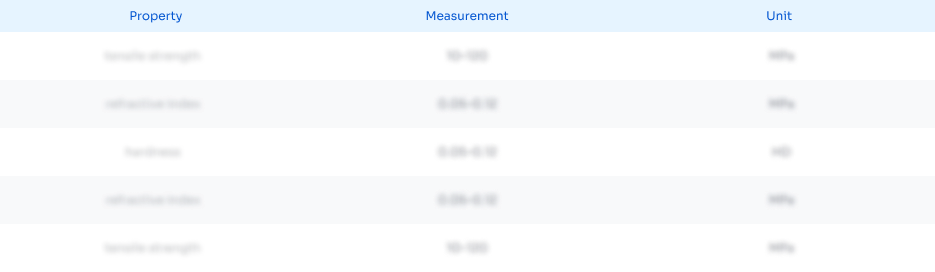
Abstract
Description
Claims
Application Information

- R&D
- Intellectual Property
- Life Sciences
- Materials
- Tech Scout
- Unparalleled Data Quality
- Higher Quality Content
- 60% Fewer Hallucinations
Browse by: Latest US Patents, China's latest patents, Technical Efficacy Thesaurus, Application Domain, Technology Topic, Popular Technical Reports.
© 2025 PatSnap. All rights reserved.Legal|Privacy policy|Modern Slavery Act Transparency Statement|Sitemap|About US| Contact US: help@patsnap.com