Loom beam yarn color weaving method and special equipment
A special equipment and yarn technology, which is applied in the field of weaving yarn dyeing and weaving yarn dyeing and weaving equipment for yarn-dyed fabrics, can solve the problems of low production efficiency of intermittent dyeing, achieve high dyeing production efficiency and reduce energy consumption. Consumption and water consumption, quality improvement effect
- Summary
- Abstract
- Description
- Claims
- Application Information
AI Technical Summary
Problems solved by technology
Method used
Image
Examples
Embodiment 1
[0037] Special equipment for weaving beam yarn dyeing, as shown in Figure 1-3, it consists of three parts: warp beam unwinding mechanism, padding mechanism and weaving beam winding mechanism. Friction roller 1, the full warp beam 2 is placed on the warp beam unwinding friction roller, the full warp beam and the warp beam unwinding friction roller are dynamically connected according to friction force, and the sheet yarn 3 in the unwinding state of multiple warp beams passes through the guide roller 4 Enter the padding unit, one of the guide rollers is fixed in the solution tank 5 of the padding mechanism, the top of the solution tank is equipped with a paddle car 6 with a driving mechanism, the paddle car and the guide roll are dynamically connected by yarn, and the paddle car drive mechanism 11 is The motor is connected to the warp beam unwinding friction roller 1 and the weaving beam winding friction roller 10 respectively through the power transmission device 7 (chain, belt o...
Embodiment 2
[0040] Adopt the processing equipment described in embodiment 1, carry out weaving beam yarn reactive dye cold pad-batch dyeing black pure cotton 32 plied yarns, dyeing formula is as follows:
[0041] Reactive black C-NN 80g / L
[0042] Penetrant TH 6g / L
[0043] Refining agent XFJ 3g / L
[0044] Caustic soda 25g / L
[0045] Sodium silicate 70g / L
[0046] After dyeing, it is stacked and fixed for about 30 hours, and the excess rate is 60%. After stacking, it is directly woven on the machine. Conventional greige finishing is sufficient, and the resulting product has uniform color, no floating color, reduced water consumption, and increased efficiency by 5 times.
Embodiment 3
[0048] Adopt the processing equipment described in embodiment 1 to carry out warp beam dyeing, can put warp beam respectively on the weaving beam rubbing roller, dye different colors as required. After dyeing, the warp beams are stacked and fixed, then put back on the warp beam friction roller, rewound into loom beams (dyeing tank without dye solution) and then weaved on the machine. Method Washing, drying, and then conventional greige finishing can be carried out, and the obtained product has uniform color and luster, no floating color, reduces water consumption, and improves efficiency by 6 times.
PUM
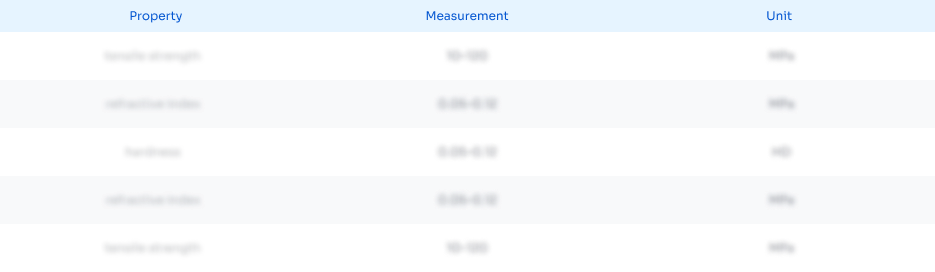
Abstract
Description
Claims
Application Information

- Generate Ideas
- Intellectual Property
- Life Sciences
- Materials
- Tech Scout
- Unparalleled Data Quality
- Higher Quality Content
- 60% Fewer Hallucinations
Browse by: Latest US Patents, China's latest patents, Technical Efficacy Thesaurus, Application Domain, Technology Topic, Popular Technical Reports.
© 2025 PatSnap. All rights reserved.Legal|Privacy policy|Modern Slavery Act Transparency Statement|Sitemap|About US| Contact US: help@patsnap.com