Method of manufacturing wiring substrate
A technology of a wiring substrate and a manufacturing method, which can be used in the manufacture of printed circuits, semiconductor/solid-state device manufacture, and catalyst-applied resists, etc., and can solve the problems of numerous manufacturing processes and the like
- Summary
- Abstract
- Description
- Claims
- Application Information
AI Technical Summary
Problems solved by technology
Method used
Image
Examples
experiment example
[0053] 3.1. The first experimental example
[0054] A wiring board is formed by the method of manufacturing a wiring board according to this embodiment.
[0055] (1) Form a photoresist film (photoresist film, photoresist film) on a glass substrate, and then, by direct writing, expose the photoresist film in the form of a straight line with a pitch of about 1 μm and a width of about 200 nm , and developed to form a photoresist layer having linear lines with a width of approximately 800 nm and stripe-shaped openings with an interval of approximately 200 nm.
[0056] (2) Next, the glass substrate was cut into a square of 1×1 cm, and immersed in a cationic surfactant solution (FPD condiishyona manufactured by Technic Japan Co., Ltd., FPD conditioner manufactured by Technic Japan Co., Ltd.), and then, The glass substrate is fully washed with water.
[0057] (3) Next, a catalyst solution was prepared by the following procedure. First, a mixed solution of hydrochloric acid, hydrog...
PUM
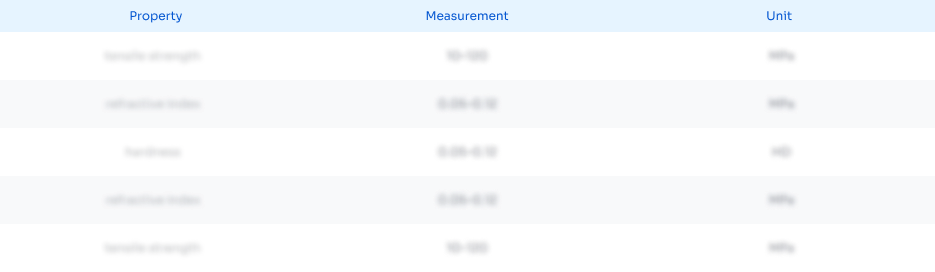
Abstract
Description
Claims
Application Information

- Generate Ideas
- Intellectual Property
- Life Sciences
- Materials
- Tech Scout
- Unparalleled Data Quality
- Higher Quality Content
- 60% Fewer Hallucinations
Browse by: Latest US Patents, China's latest patents, Technical Efficacy Thesaurus, Application Domain, Technology Topic, Popular Technical Reports.
© 2025 PatSnap. All rights reserved.Legal|Privacy policy|Modern Slavery Act Transparency Statement|Sitemap|About US| Contact US: help@patsnap.com