Poured material for foundry ladle bottom and its pouring process and mold
A castable and molten iron technology, which is used in molds, manufacturing tools, cement mixing devices, etc., can solve the problems of low medium and high temperature strength, high water content, and low service life, and achieve high medium and high temperature strength, low water content, Effect of bottom radian specification
- Summary
- Abstract
- Description
- Claims
- Application Information
AI Technical Summary
Problems solved by technology
Method used
Image
Examples
Embodiment Construction
[0011] According to the requirements for the use of refractory materials at the bottom of molten iron tanks at home and abroad, the physical and chemical indicators of castables at the bottom of molten iron tanks are shown in Table 1:
[0012] Table 1 Physicochemical indicators of bottom pouring of molten iron tanks
[0013]
project
al 2 o 3
(%)
Refractoriness
(℃)
Compressive strength (MPa)
1300℃×3h
Bulk density (g / cm 3 )
110℃×24h
standard value
≥60
≥1790
≥35
≥2.5
[0014] According to the above requirements, considering the matching of tank bottom castables and tank body refractory bricks (high alumina bricks), select super-grade bauxite aggregates, corundum, silica powder, magnesia, admixtures, etc. The main components and weight percentages are shown in Table 2; See Table 3 for the weight percentage of the original castable components.
[0015] ...
PUM
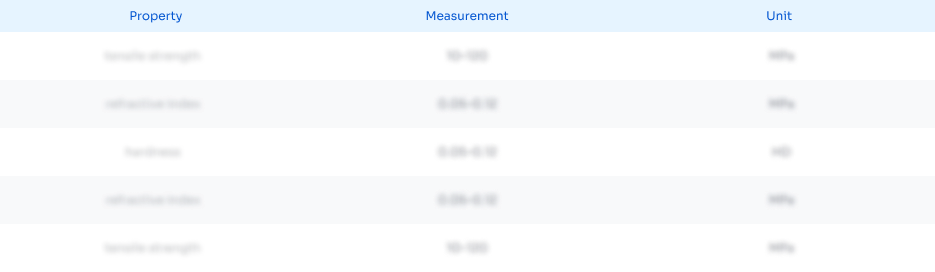
Abstract
Description
Claims
Application Information

- R&D
- Intellectual Property
- Life Sciences
- Materials
- Tech Scout
- Unparalleled Data Quality
- Higher Quality Content
- 60% Fewer Hallucinations
Browse by: Latest US Patents, China's latest patents, Technical Efficacy Thesaurus, Application Domain, Technology Topic, Popular Technical Reports.
© 2025 PatSnap. All rights reserved.Legal|Privacy policy|Modern Slavery Act Transparency Statement|Sitemap|About US| Contact US: help@patsnap.com