Rolled heat exchanger
A heat exchanger and winding technology, applied in the field of winding heat exchangers, can solve problems such as expensive, high inertia, and troublesome manufacturing
- Summary
- Abstract
- Description
- Claims
- Application Information
AI Technical Summary
Problems solved by technology
Method used
Image
Examples
Embodiment Construction
[0026] figure 1 shows a top view of a conventional liquid distributor for a wound heat exchanger used, for example, as a liquefier in an LNG base-type production plant. The liquid distributor has three pie-segment-shaped perforated bottom plates 1 which are arranged uniformly around the core tube 2 of the heat exchanger and extend as far as the cylindrical shell 3 of the heat exchanger. A plurality of tubes are wound on the core tube 2 and are guided through the distributor in the open regions 4 between the individual perforated base plates 1 .
[0027] The perforated bottom plate 1 is provided with a plurality of drip openings 5 through which the liquid on the perforated bottom plate 1 can drip onto the tube bundle located below.
[0028] The supply of liquid takes place via a ring pre-distributor as in the figure 2 and image 3 as shown schematically. The annular predistributor has a lateral liquid inlet 6 which opens into a surge tank 7 . The side 8 of the buffer bo...
PUM
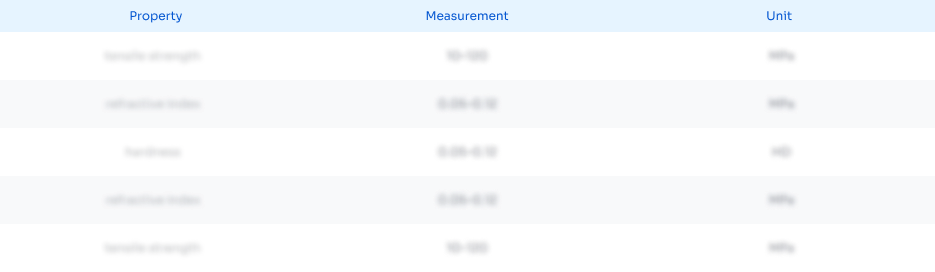
Abstract
Description
Claims
Application Information

- R&D
- Intellectual Property
- Life Sciences
- Materials
- Tech Scout
- Unparalleled Data Quality
- Higher Quality Content
- 60% Fewer Hallucinations
Browse by: Latest US Patents, China's latest patents, Technical Efficacy Thesaurus, Application Domain, Technology Topic, Popular Technical Reports.
© 2025 PatSnap. All rights reserved.Legal|Privacy policy|Modern Slavery Act Transparency Statement|Sitemap|About US| Contact US: help@patsnap.com