Method for preparing alloy of vanadium nitride
A technology of vanadium nitride alloy and vanadium compound is applied in the production field of vanadium nitride alloy, which can solve the problems of large energy consumption and furnace body loss, affecting the effective diffusion of nitrogen, and high production cost, saving energy and reducing equipment investment costs. , the effect of low carbon content
- Summary
- Abstract
- Description
- Claims
- Application Information
AI Technical Summary
Problems solved by technology
Method used
Examples
Embodiment 1
[0024] Weigh equivalent to V 2 o 5 Amount of 11% activated carbon, with V 2 o 5 Mix well. Lay the mixed material in a thin layer on the feeder tray of the multi-layer tray structure, and the automatic device pushes the feeder cart into the pre-reduction section. Feed flowing NH into the preparation furnace 3 -N 2Mixed gas, the nitrogen gas integral fraction in the mixed gas is 5%, the temperature is raised to 600-650°C, and after holding for 0.5 hours, the feed truck enters the nitriding section, the temperature rises to 710-770°C, and the heat preservation is held for 8 hours. The feed car enters the cooling section, and is automatically released after being cooled to 60°C under the protection of flowing mixed gas to obtain vanadium nitride alloy powder containing 78.2% vanadium, 18.07% nitrogen, and 6.22% carbon.
Embodiment 2
[0026] Weigh equivalent to NH 4 VO 3 The amount of 4.5% charcoal powder, with NH 4 VO 3 After fully mixing and evenly laying on the material tray of the feeding car, the feeding car enters the pre-reduction section of the preparation furnace. Access to NH 3 -N 2 Mixed gas, the integral fraction of nitrogen gas in the mixed gas is 1%, the furnace temperature rises to 450-500°C and keeps constant for 0.5 hours; then enters the nitriding section, the temperature is 750-820°C, keeps warm for 6 hours, and cools to 80°C in the cooling section Automatically baked. The powder contains 78.3% vanadium, 15.12% nitrogen and 2.98% carbon.
Embodiment 3
[0028] Weigh graphite powder equivalent to 8% of the weight of ammonium polyvanadate, fully mix it with ammonium polyvanadate, spread it on the feeding tray of the feeding cart, and push the feeding cart into the pre-reduction section of the preparation furnace. Access to NH 3 Gas, the furnace temperature rises to 550-600 ℃ for 1 hour; then enters the nitriding section, the temperature is 780-840 ℃, keeps the temperature for 4.5 hours, and then automatically comes out of the furnace after cooling to 120 ℃ in the cooling section. The powder contains 77.8% vanadium, 13.51% nitrogen and 5.48% carbon.
PUM
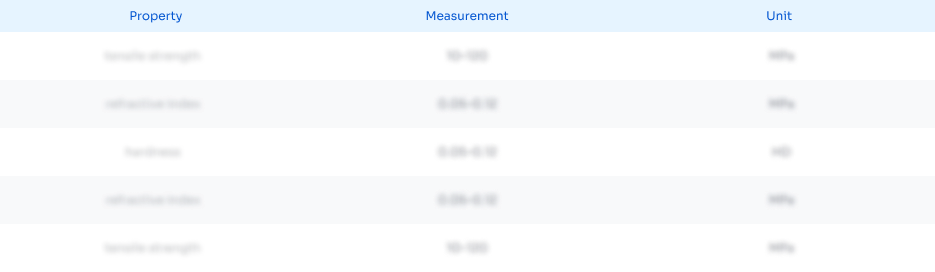
Abstract
Description
Claims
Application Information

- Generate Ideas
- Intellectual Property
- Life Sciences
- Materials
- Tech Scout
- Unparalleled Data Quality
- Higher Quality Content
- 60% Fewer Hallucinations
Browse by: Latest US Patents, China's latest patents, Technical Efficacy Thesaurus, Application Domain, Technology Topic, Popular Technical Reports.
© 2025 PatSnap. All rights reserved.Legal|Privacy policy|Modern Slavery Act Transparency Statement|Sitemap|About US| Contact US: help@patsnap.com