Welding method of vacuum tube central fulcrum bar component
A welding method and vacuum tube technology, applied in welding equipment, metal processing equipment, manufacturing tools, etc., can solve the problems of molybdenum cap falling off and high scrap rate of central rod components, and achieve high pass rate, simple and convenient design, and good performance Effect
- Summary
- Abstract
- Description
- Claims
- Application Information
AI Technical Summary
Problems solved by technology
Method used
Image
Examples
Embodiment
[0013] The welding method of the central rod assembly of the vacuum tube of the present invention comprises the following steps:
[0014] 1) Set up a counterbore 3 on the molybdenum cap 1;
[0015] 2) Add silicon molybdenum solder sheet 4 in the counterbore 3;
[0016] 3) Insert the molybdenum rod 2 into the counterbore 3;
[0017] 4) Weld the molybdenum rod 2 and the molybdenum cap 1 at the counterbore 3 by high-frequency welding
[0018] 5) The molybdenum cap and the molybdenum rod are welded by resistance welding at the mouth 5 of the molybdenum cap.
PUM
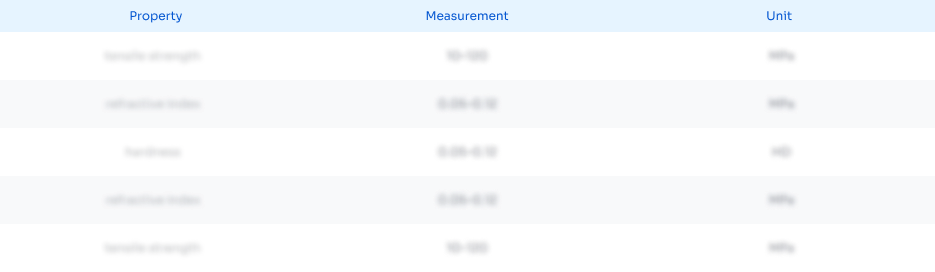
Abstract
Description
Claims
Application Information

- R&D Engineer
- R&D Manager
- IP Professional
- Industry Leading Data Capabilities
- Powerful AI technology
- Patent DNA Extraction
Browse by: Latest US Patents, China's latest patents, Technical Efficacy Thesaurus, Application Domain, Technology Topic, Popular Technical Reports.
© 2024 PatSnap. All rights reserved.Legal|Privacy policy|Modern Slavery Act Transparency Statement|Sitemap|About US| Contact US: help@patsnap.com