Process for heating titanium oblique perforating rod ingot
A technology of cross-rolling piercing and heating process, which is applied to the improvement of process efficiency, heat treatment furnaces, manufacturing tools, etc., can solve the problems of many operators, uneven heating of billets, high labor intensity, etc. No flammable and explosive substances, good for environmental protection
- Summary
- Abstract
- Description
- Claims
- Application Information
AI Technical Summary
Problems solved by technology
Method used
Image
Examples
Embodiment Construction
[0040] The heating process of the titanium cross-rolled perforated bar billet of the present invention adopts a horizontal step-by-step intermediate frequency induction heating furnace to replace the traditional inclined-bottom type gas furnace, and is used for heating the cross-rolled perforated titanium billet. The heating furnace is equipped with an automatic feeding and discharging mechanism, and the heating process is automatically carried out according to the set program and production cycle requirements.
[0041] The technical principle of the step horizontal type intermediate frequency induction heating furnace of the present invention is:
[0042] The coil is used to convert the alternating current into an induced current through an alternating magnetic field to heat the metal titanium rod. By continuously adjusting the frequency of the alternating current and the input power, the heat dissipation on the surface of the metal bar and the heat transfer to the core of th...
PUM
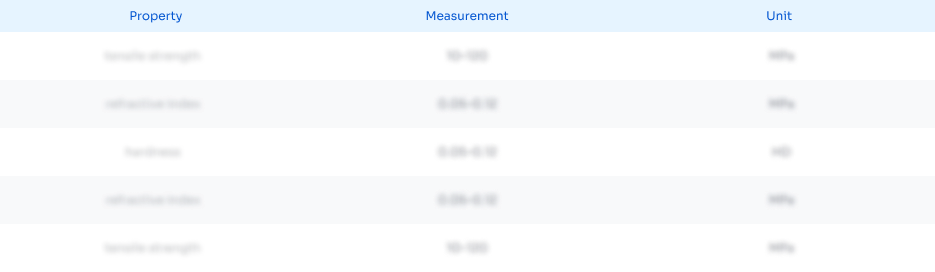
Abstract
Description
Claims
Application Information

- R&D
- Intellectual Property
- Life Sciences
- Materials
- Tech Scout
- Unparalleled Data Quality
- Higher Quality Content
- 60% Fewer Hallucinations
Browse by: Latest US Patents, China's latest patents, Technical Efficacy Thesaurus, Application Domain, Technology Topic, Popular Technical Reports.
© 2025 PatSnap. All rights reserved.Legal|Privacy policy|Modern Slavery Act Transparency Statement|Sitemap|About US| Contact US: help@patsnap.com