Method for treating white residue
A treatment method and technology for silicon slag, applied in the removal of solid waste, alumina/aluminum hydroxide, etc., can solve the problems of unreasonable economy, too harsh equipment material requirements, high alkali concentration, and achieve economical and reasonable recovery, equipment material Low demand, high recovery effect
- Summary
- Abstract
- Description
- Claims
- Application Information
AI Technical Summary
Problems solved by technology
Method used
Image
Examples
Embodiment 1
[0020] 1. Production process conditions:
[0022] The moisture content of mixed silicon slag slurry is 46%
[0023] Silicon slag raw material [N] / [R]([N] / [R]=[Na 2 O] / [Fe 2 o 3 ]+[Al 2 o 3 ]) 1.0
[0024] Silicon slag raw material [C] / [S]([C] / [S]=[CaO] / [SiO 2 ]) 1.6
[0025] 2. Clinker sintering
[0026] Silicon slag clinker sintering temperature 1000°C
[0027] Sintering time 30~60s
[0028] 3. Dissolution of clinker
[0029] Dissolution temperature 85℃
[0030] Dissolution L / S 4-4.5
[0031] Dissolution time 30min
[0032] 2. Technical indicators:
[0033] Standard dissolution rate of silicon slag clinker: Al 2 o 3 95.25%
[0034] Na 2 O 96.6%
[0035] Net dissolution rate of silicon slag clinker: Al 2 o 3 89.48%
[0036] Na 2 O 95.19%
[0037] Red mud settlement index:
[0038]
Embodiment 2
[0040] 1. Production process conditions:
[0041] 1. Silicon slag slurry
[0042] The moisture content of mixed silicon slag slurry is 46%
[0043] Silicon slag raw meal [N] / [R] 0.92
[0044] Silicon slag raw meal [C] / [S] 1.7
[0045] 2. Clinker sintering
[0046] Silicon slag clinker sintering temperature 1050°C
[0047] Sintering time 30~60s
[0048] 3. Dissolution of clinker
[0049] Dissolution temperature 85℃
[0050] Dissolution L / S 4-4.5
[0051] Dissolution time 30min
[0052] 2. Technical indicators:
[0053] Standard dissolution rate of silicon slag clinker: Al 2 o 395.48%
[0054] Na 2 O 96.8%
[0055] Net dissolution rate of silicon slag clinker: Al 2 o 3 90.12%
[0056] Na 2 O 95.84%
[0057] Red mud settlement index:
[0058]
Embodiment 3
[0060] 1. Production process conditions:
[0061] 1. Silicon slag slurry
[0062] The moisture content of mixed silicon slag slurry is 46%
[0063] Silicon slag raw meal [N] / [R] 0.98
[0064] Silicon slag raw meal [C] / [S] 1.35
[0065] 2. Clinker sintering
[0066] Silicon slag clinker sintering temperature 1100℃
[0067] Sintering time 30~60s
[0068] 3. Dissolution of clinker
[0069] Dissolution temperature 85℃
[0070] Dissolution solid-liquid ratio L / S 4-4.5
[0071] Dissolution time 30min
[0072] 2. Technical indicators:
[0073] Standard dissolution rate of silicon slag clinker: Al 2 o 3 95.95%
[0074] Na 2 O 97.2%
[0075] Net dissolution rate of silicon slag clinker: Al 2 o 3 90.89%
[0076] Na 2 O 95.88%
[0077] Red mud settlement index:
[0078]
PUM
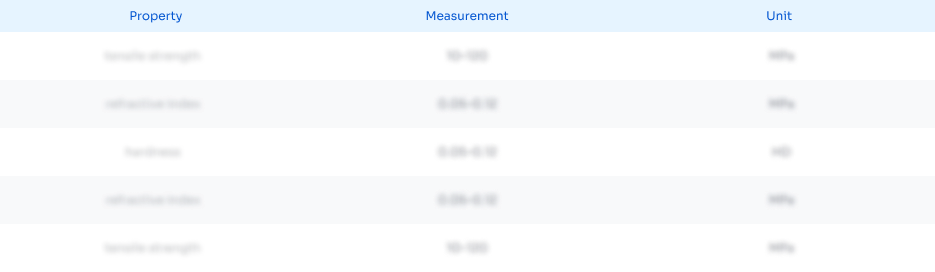
Abstract
Description
Claims
Application Information

- Generate Ideas
- Intellectual Property
- Life Sciences
- Materials
- Tech Scout
- Unparalleled Data Quality
- Higher Quality Content
- 60% Fewer Hallucinations
Browse by: Latest US Patents, China's latest patents, Technical Efficacy Thesaurus, Application Domain, Technology Topic, Popular Technical Reports.
© 2025 PatSnap. All rights reserved.Legal|Privacy policy|Modern Slavery Act Transparency Statement|Sitemap|About US| Contact US: help@patsnap.com