Battery differential thickness steel casing and its manufacturing technique
A production process and steel shell technology, applied in the field of battery differential thickness steel shell and its production process, can solve the problems such as the wall thickness can be moderately reduced, the wall thickness cannot be reduced, etc., to achieve stable product quality, high production efficiency, increase in The effect of filling
- Summary
- Abstract
- Description
- Claims
- Application Information
AI Technical Summary
Problems solved by technology
Method used
Image
Examples
Embodiment 1
[0031] Example 1 as figure 1 Shown: a steel case with poor thickness of the battery, which is a hollow cylinder with the positive head 1 closed and the shell mouth 3 enlarged and open. The outer surface of the hollow cylinder is a cylindrical surface, and the thinnest wall thickness of the middle section 2 of the hollow cylinder is 0.18mm, which is smaller than the wall thickness of the positive electrode head 1 and the shell mouth 3 of 0.25mm.
[0032] The thickness of each part of the steel shell of the existing alkaline battery with equal thickness structure is 0.25mm, and the thickness of the steel shell of the battery is reduced from 0.25mm to 0.18mm under the premise of maintaining the strength requirement; The inner cavity space of the casing is increased, and the volume of the cylinder is increased by 4%, thereby increasing the filling amount of the active material, improving the discharge performance of the battery, and prolonging the service life.
Embodiment 2
[0033] Example 2 as Figure 2-3 Shown: A production process of a steel case with a different thickness of the battery is processed sequentially along the following stations on a multi-station automatic punching machine;
[0034] [1] According to the size required by the steel shell blank, the raw material is punched and cut into a disc and shallow stretched into a bowl shape;
[0035] [2] Transition station, no action;
[0036] [3] Shallow stretching, the first time to reduce the diameter of the blank and increase the height;
[0037] [4] Shallow stretching, the second time to reduce the diameter of the blank and increase the height;
[0038] [5] Retain the wall thickness of the positive head 1, stretch the hollow cylinder, and reduce the wall thickness of the middle section 2 of the hollow cylinder;
[0039] [6] Deep drawing the hollow cylinder, reducing the diameter, increasing the height, and reducing the wall thickness of the middle section 2 of the hollow cylinder;
...
PUM
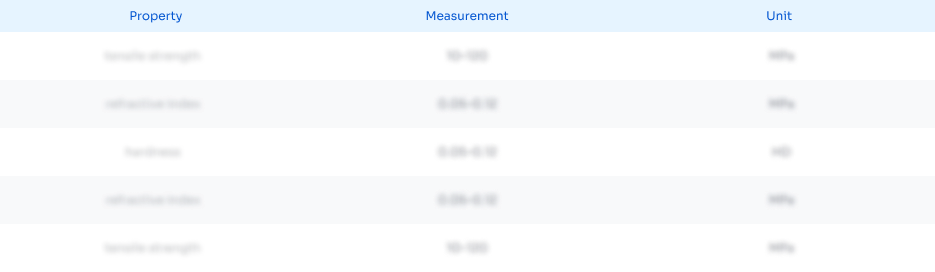
Abstract
Description
Claims
Application Information

- Generate Ideas
- Intellectual Property
- Life Sciences
- Materials
- Tech Scout
- Unparalleled Data Quality
- Higher Quality Content
- 60% Fewer Hallucinations
Browse by: Latest US Patents, China's latest patents, Technical Efficacy Thesaurus, Application Domain, Technology Topic, Popular Technical Reports.
© 2025 PatSnap. All rights reserved.Legal|Privacy policy|Modern Slavery Act Transparency Statement|Sitemap|About US| Contact US: help@patsnap.com