Antistatic leather and its preparing method
An antistatic and leather technology, applied in the field of leather, can solve the problems of affecting the aesthetics and hygienic properties of leather, affecting the adhesion of the coating, and the effect is not ideal, and achieves the effects of high mechanical strength, high absorption and low price.
- Summary
- Abstract
- Description
- Claims
- Application Information
AI Technical Summary
Problems solved by technology
Method used
Image
Examples
Embodiment 2
[0012] Example 2: first put the raw skin in the drum and soak it in water for 12 hours. After the raw skin is fully softened, adjust the liquid ratio to 2.0 and then add sodium sulfide so that the concentration of sodium sulfide is 5 grams per liter, and continue to soak in the drum. After turning for 1.8 hours, add 3.8% of the weight of the raw hide with a mass concentration of 30% sodium hydroxide, continue to turn for 1 hour, then wash with water, deash, and soften; secondly, adjust the liquid ratio to 1.0, and add the raw hide to the softened raw hide 14% salt by weight rotated for 10 minutes, then added 1.2% of the mass concentration of raw hide weight from the shaft hole as 98% sulfuric acid and 1.6% of the raw hide weight by 37% acetic acid and rotated for 1.5 hours, and tanned with iron tanning agent at room temperature 3 hours, stand still for 12 hours, planing, shaving, weighing, retanning with acrylic resin retanning agent for 5 hours, adjust the liquid ratio to 1.5,...
Embodiment 3
[0013] Example 3: first place the raw skin in the drum and soak it in water for 18 hours. After the raw skin is fully softened, adjust the liquid ratio to 1.3 and then add sodium sulfide so that the concentration of sodium sulfide is 8 grams per liter, and continue to soak in the drum. After turning for 1.6 hours, add 4.2% of the weight of raw hide with a mass concentration of 30% sodium hydroxide, continue to turn for 1 hour, then wash with water, deash, and soften; then adjust the liquid ratio to 1.2, and add raw hide to the softened raw hide 10% by weight of salt and rotated for 10 minutes, then add 1.4% of the mass concentration of raw hide weight as 98% sulfuric acid and 1.2% of raw hide weight from the shaft hole as 37% acetic acid and rotate for 1.0 hour, and tan with iron tanning agent at room temperature 3 hours, stand still for 12 hours, planing, shaving, weighing, retanning with acrylic resin retanning agent for 6 hours, adjust the liquid ratio to 1.1, and then add 1...
Embodiment 4
[0014] Example 4: First put the raw skin in the drum and soak it in water for 24 hours. After the raw skin is fully softened, adjust the liquid ratio to 1.7 and then add sodium sulfide so that the concentration of sodium sulfide is 9 grams per liter, and continue to soak in the drum. After turning for 2 hours, add 4.5% of the weight of raw hide with a mass concentration of 30% sodium hydroxide, continue to turn for 1 hour, then wash with water, deash, and soften; secondly, adjust the liquid ratio to 1.5, and add raw hide to the softened raw hide 15% by weight of salt and rotated for 10 minutes, then add 1.5% of the weight of the raw hide from the shaft hole with a mass concentration of 98% sulfuric acid and 2% of the weight of the raw hide with a mass concentration of 37% acetic acid, rotate for 0.8 hours, and tan with an iron tanning agent at room temperature 3 hours, stand still for 12 hours, planed, shaved, weighed, and then retanned with acrylic resin retanning agent for 4 ...
PUM
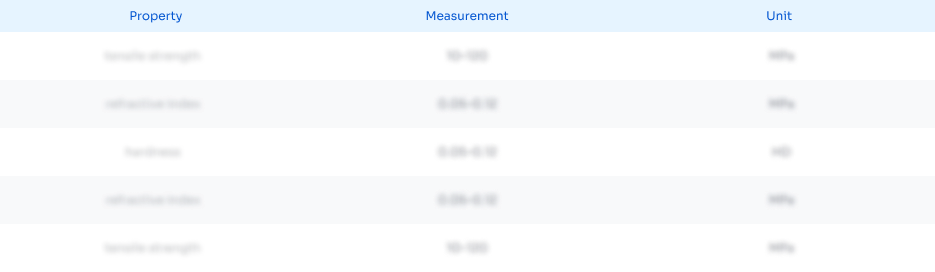
Abstract
Description
Claims
Application Information

- R&D Engineer
- R&D Manager
- IP Professional
- Industry Leading Data Capabilities
- Powerful AI technology
- Patent DNA Extraction
Browse by: Latest US Patents, China's latest patents, Technical Efficacy Thesaurus, Application Domain, Technology Topic, Popular Technical Reports.
© 2024 PatSnap. All rights reserved.Legal|Privacy policy|Modern Slavery Act Transparency Statement|Sitemap|About US| Contact US: help@patsnap.com