Method for increasing tar yield of coalite pyrolysis with methane as reaction gas
A technology of tar yield and reaction gas, which is applied in the petroleum industry and the preparation of liquid hydrocarbon mixtures, etc., can solve the problems of inability to recover semi-coke catalysts, and can not significantly increase the tar yield, so as to reduce the cost of hydropyrolysis and facilitate The effect of recycling
- Summary
- Abstract
- Description
- Claims
- Application Information
AI Technical Summary
Problems solved by technology
Method used
Image
Examples
Embodiment 1
[0022] The selected catalyst is Ni / Al 2 o 3 Catalyst, its preparation method is: at 20-60 purpose Al 2 o 3 impregnated with 10% (weight percent) Ni(NO 3 ) 2 6H 2 O, dried at 100°C for 5 hours, calcined at 800°C for 8 hours, H at 700°C 2 Restore 10min;
[0023] The selected coal is Yanzhou coal, and its industrial analysis and elemental analysis are shown in Table 1. The test uses 5g of coal, 1g of catalyst, the pyrolysis conditions are temperature 700°C, constant temperature time 30min, pressure 2.0MPa, reaction gas 400ml / min CH 4 and 100ml / min air are mixed through the methane inlet C and the oxidant inlet D respectively, and then enter the reactor through the gas inlet A. The mixed gas passes through the catalyst layer 2 for activation reaction and enters the coal pyrolysis reaction layer 1 through the gas distribution plate 3 . The coal and reaction gases are co-pyrolyzed in a pressurized fixed-bed reactor. The liquid product generated by pyrolysis is taken out of ...
Embodiment 2
[0025] The selected catalyst is Ni / Al 2 o 3 Catalyst, its preparation method is: at 20-60 purpose Al 2 o 3 impregnated with 10% (weight percent) Ni(NO 3 )2 6H 2 O, dried at 100°C for 5 hours, calcined at 800°C for 8 hours, H at 700°C 2 Restore 10min;
[0026] The selected coal is Yanzhou coal, and its industrial analysis and elemental analysis are shown in Table 1. The test uses 5g of coal, 1g of catalyst, the pyrolysis conditions are temperature 700°C, constant temperature time 30min, pressure 2.0MPa, reaction gas 400ml / min CH 4 and 100ml / min oxygen are respectively mixed through methane inlet C and oxidant inlet D, and then enter the reactor through gas inlet A, and the mixed gas passes through catalyst layer 2 for activation reaction and enters coal pyrolysis reaction layer 1 through gas distribution plate 3. The coal and reaction gases are co-pyrolyzed in a pressurized fixed-bed reactor. The liquid product generated by pyrolysis is taken out of the reactor by the r...
Embodiment 3
[0028] The selected catalyst is Ni / Al 2 o 3 Catalyst, its preparation method is: at 20-60 purpose Al 2 o 3 impregnated with 10% (weight percent) Ni(NO 3 ) 2 6H 2 O, dried at 100°C for 5 hours, calcined at 800°C for 8 hours, H at 700°C 2 Restore 10min;
[0029] Pyrolysis: The pyrolysis reactor is shown in the figure. The reactor is divided into upper and lower layers. One end of the gas inlet is the catalyst layer 2, and the other end is the coal seam 1, separated by a gas distribution plate 3 in the middle.
[0030] The selected coal is Yanzhou coal, and its industrial analysis and elemental analysis are shown in Table 1. The test uses 5g of coal, 1g of catalyst, the pyrolysis conditions are temperature 600°C, constant temperature time 30min, pressure 2.0MPa, reaction gas 400ml / min CH 4 and 100ml / min oxygen are respectively mixed through methane inlet C and oxidant inlet D, and then enter the reactor through gas inlet A. The mixed gas passes through the catalyst layer ...
PUM
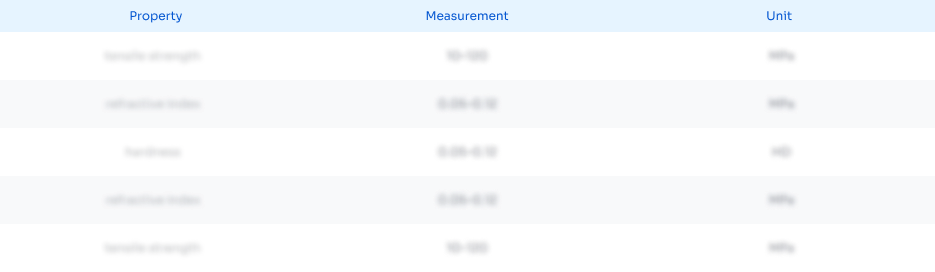
Abstract
Description
Claims
Application Information

- R&D
- Intellectual Property
- Life Sciences
- Materials
- Tech Scout
- Unparalleled Data Quality
- Higher Quality Content
- 60% Fewer Hallucinations
Browse by: Latest US Patents, China's latest patents, Technical Efficacy Thesaurus, Application Domain, Technology Topic, Popular Technical Reports.
© 2025 PatSnap. All rights reserved.Legal|Privacy policy|Modern Slavery Act Transparency Statement|Sitemap|About US| Contact US: help@patsnap.com