Phenol formaldehyde-rubber copolymerized emulsion and its preparation method
A rubber copolymerization and emulsion technology, applied in textiles, papermaking, fiber processing, etc., can solve the problems of short storage time of latex, enhanced bending fatigue performance of rubber products, RF resin reaction, etc., to increase the safety and operability of use, The effect of improving static and dynamic fatigue performance, improving bending fatigue performance
- Summary
- Abstract
- Description
- Claims
- Application Information
AI Technical Summary
Problems solved by technology
Method used
Examples
Embodiment 1
[0029] Embodiment 1, phenolic-rubber copolymer emulsion is made by following dry weight (gram) proportioning raw material:
[0030] (1), from resorcinol formaldehyde resin: mixed latex (mixture of butylpyridine latex and chloroprene latex): formaldehyde = 10: 100: 1.2
[0031] Among them, butylpyridine latex: neoprene latex = 6: 2 or
[0032] (2), by resorcinol formaldehyde resin: mixed latex (butadiene latex, chloroprene latex, the mixture of carboxyl styrene-butadiene latex and acrylate latex): formaldehyde=10:100:0.8, wherein butylpyramid latex: chloroprene Latex: carboxylated styrene-butadiene latex: acrylate latex = 5:3:1:1, or
[0033] (3), by resorcinol formaldehyde resin: mixed latex (by the mixture of butylpyrrolate latex, chloroprene latex, carboxyl styrene-butadiene latex and natural rubber latex): formaldehyde donor=15:100:1.2,
[0034] Among them, butylpyridine latex: neoprene latex: carboxylated styrene-butadiene latex: natural rubber latex = 5:3:1:1.
Embodiment 2
[0035] Embodiment 2, a kind of preparation method of phenolic-rubber copolymer emulsion, concrete preparation steps are as follows:
[0036] The first step: in a reactor placed in a constant temperature water bath, weigh 6.7 grams of resorcinol and place it in the reactor, fully dissolve it with 87.1 grams of soft water, then add 0.27 grams of sodium hydroxide, and stir well Simultaneously, add dropwise 3.5 grams of 37% formaldehyde solution in the ratio of 1 / 0.7 by resorcinol / formaldehyde (R / F) molar ratio, control the concentration of RF resin at 8%, control reaction temperature at 25 ± 1 ℃, pass acidity Meter controls the final pH value of the RF resin to reduce the value to 0.4, and the reaction time is about 6 hours to obtain 100 grams of precondensed resorcinol formaldehyde resin;
[0037]Step 2: According to the ratio of 5:4:1, weigh the butylpyrrolate latex, chloroprene latex, and carboxylated styrene-butadiene latex respectively. After diluting the latex with 20%-50% ...
Embodiment 3
[0040] Weigh 5.8 grams of resorcinol and put it into a reaction vessel, dissolve it with 86.3 grams of soft water, add 0.2 grams of NaOH, mix it evenly, then weigh 3.9 grams of 37% formaldehyde and add it to a reaction vessel in a 35°C water bath After stirring evenly, when the pH value decreased to 1.0, 100 grams of resorcinol formaldehyde resin was obtained. According to the ratio of RF / L=10 / 100, this resorcinol formaldehyde resin is added to the latex mixed with butylpyridine latex, chloroprene latex, and carboxylated styrene-butadiene latex at a dry rubber weight ratio of 6:4:0 to carry out The copolymerization reaction is 20 hours, and the storage time of the prepared RFL emulsion is generally more than 96 hours. Add 1.2 grams of 37% before use. At this time, the RFL film has a certain toughness. Use it to treat glass fibers, and the monofilament isolation of glass fibers Good, the mechanical properties of glass fiber rope are high, but the adhesion and performance after ...
PUM
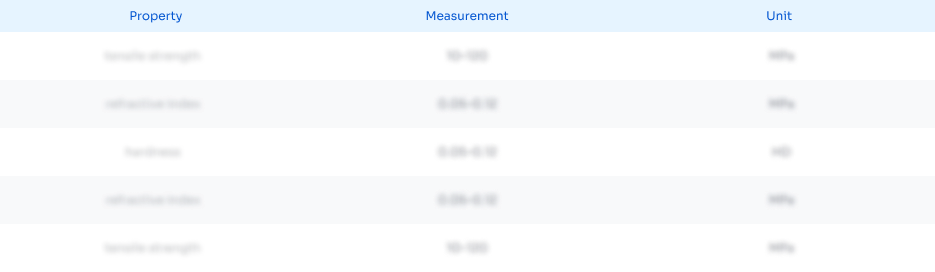
Abstract
Description
Claims
Application Information

- R&D
- Intellectual Property
- Life Sciences
- Materials
- Tech Scout
- Unparalleled Data Quality
- Higher Quality Content
- 60% Fewer Hallucinations
Browse by: Latest US Patents, China's latest patents, Technical Efficacy Thesaurus, Application Domain, Technology Topic, Popular Technical Reports.
© 2025 PatSnap. All rights reserved.Legal|Privacy policy|Modern Slavery Act Transparency Statement|Sitemap|About US| Contact US: help@patsnap.com