Method for forging combined forged steel coupler yoke for railway vehicles
A railway vehicle and coupler frame technology, which is applied in the forging field of combined forged steel coupler frames, can solve the problems such as the difficulty of the overall forged steel coupler frame process, the heavy machining workload, and the low utilization rate of materials. Achieve the effects of reducing machining allowance, reducing workload and high material utilization
- Summary
- Abstract
- Description
- Claims
- Application Information
AI Technical Summary
Problems solved by technology
Method used
Image
Examples
Embodiment Construction
[0025] The process steps of the method of the present invention will be described in detail below in conjunction with the accompanying drawings and specific embodiments.
[0026] Such as Figure 1 to Figure 5 As shown, take the manufacture of railway coupler yoke frame No. 17 as an example. The yoke frame is a frame-type thin-walled structure with a minimum wall thickness of 28mm and a minimum height of 140mm. The square hole in the head cannot be forged, and the draft angle needs to be machined. , the workload of machining is large, the utilization rate of materials is low, the weight of the coupler frame is 97.5Kg, and it must be forged on a 16t hammer or other large die forging equipment. The manufacturing steps are:
[0027] (1) Blanking to obtain a blank of a certain length.
[0028] (2) Blank making, after the blank obtained by cutting is heated, it is drawn and blanked on the free forging anvil, so that the blank is initially deformed, and the shape and size are close ...
PUM
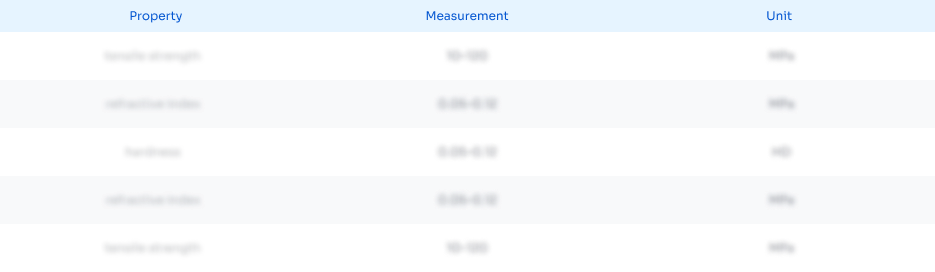
Abstract
Description
Claims
Application Information

- R&D
- Intellectual Property
- Life Sciences
- Materials
- Tech Scout
- Unparalleled Data Quality
- Higher Quality Content
- 60% Fewer Hallucinations
Browse by: Latest US Patents, China's latest patents, Technical Efficacy Thesaurus, Application Domain, Technology Topic, Popular Technical Reports.
© 2025 PatSnap. All rights reserved.Legal|Privacy policy|Modern Slavery Act Transparency Statement|Sitemap|About US| Contact US: help@patsnap.com