Polyurethane resin for synthetic leather and porous sheet material
A technology of polyurethane resin and synthetic leather, applied in textiles and papermaking, etc., can solve the problems of high crystallinity, poor low temperature characteristics and hard texture of polycarbonate diol
- Summary
- Abstract
- Description
- Claims
- Application Information
AI Technical Summary
Problems solved by technology
Method used
Image
Examples
Embodiment 1
[0096]In a four-necked flask with a stirrer and a thermometer, add 3-methyl-pentanediol / 1,6-hexanediol (mole percent: 30 / 70) with a number average molecular weight of 2,000 (calculated from the hydroxyl value) to copolymerize Copolymerization of 60 parts of polycarbonate diol, 1,9-nonanediol / 2-methyl-1,8-octanediol (mole percent: 15 / 85) with a number average molecular weight of 2,000 (calculated from the hydroxyl value) 140 parts of polycarbonate diols, 12.7 parts of ethylene glycol (hereinafter referred to as EG), 77.5 parts of MDI and 677 parts of DMF were reacted at 70°C for 15 hours in a dry nitrogen atmosphere to obtain a resin concentration of 30%, a viscosity of It is a polyurethane resin (D-1) solution at 90,000 mPa s / 20°C and a solidification value of 3.3.
Embodiment 2
[0098] In the same reaction vessel as in Example 1, 3-methyl-pentanediol / 1,6-hexanediol (mole percent: 30 / 70) copolymerized with a number average molecular weight of 2,000 (calculated from the hydroxyl value) was added. Copolymerization of 100 parts of carbonate diol, 1,9-nonanediol / 2-methyl-1,8-octanediol (mole percent: 15 / 85) with a number average molecular weight of 2,000 (calculated from the hydroxyl value) 100 parts of carbonate diol, 15.2 parts of 1,4-butanediol (hereinafter referred to as 1,4-BG), 68.5 parts of MDI and 662 parts of DMF were reacted at 65°C for 20 hours in a dry nitrogen atmosphere to obtain A polyurethane resin (D-2) solution with a resin concentration of 30%, a viscosity of 85,000 mPa s / 20°C, and a solidification value of 4.3.
Embodiment 3
[0100] In the same reaction vessel as in Example 1, 3-methyl-pentanediol / 1,6-hexanediol (mole percent: 50 / 50) copolymerized with a number average molecular weight of 2,000 (calculated from the hydroxyl value) was added. Copolymerization of 1,9-nonanediol / 2-methyl-1,8-octanediol (mole percent: 15 / 85) with 80 parts of carbonate diol and a number average molecular weight of 2,000 (calculated from the hydroxyl value) 120 parts of carbonate diol, 19.2 parts of 1,4-BG, 79.8 parts of MDI and 698 parts of DMF were reacted at 65°C for 20 hours in a dry nitrogen atmosphere to obtain a resin with a concentration of 30% and a viscosity of 80,000mPa s / 20 ℃, solidification value of 3.8 polyurethane resin (D-3) solution.
PUM
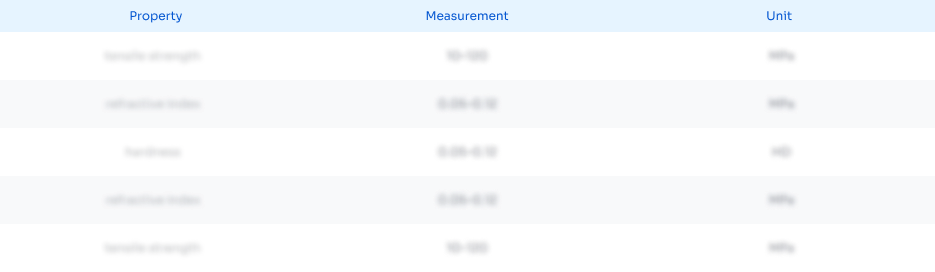
Abstract
Description
Claims
Application Information

- R&D
- Intellectual Property
- Life Sciences
- Materials
- Tech Scout
- Unparalleled Data Quality
- Higher Quality Content
- 60% Fewer Hallucinations
Browse by: Latest US Patents, China's latest patents, Technical Efficacy Thesaurus, Application Domain, Technology Topic, Popular Technical Reports.
© 2025 PatSnap. All rights reserved.Legal|Privacy policy|Modern Slavery Act Transparency Statement|Sitemap|About US| Contact US: help@patsnap.com