Method for melting cast aluminum alloy
A technology for casting aluminum alloys and aluminum-silicon alloys, applied in the field of aluminum alloy smelting, can solve the problems of increasing alloy gas absorption and iron increase, alloy element burning loss, increased composition fluctuation, and long smelting time, so as to reduce smelting iron increase , operation time is shortened, and the effect of prolonged exposure is reduced
- Summary
- Abstract
- Description
- Claims
- Application Information
AI Technical Summary
Problems solved by technology
Method used
Examples
Embodiment 1
[0045] Cast aluminum alloy smelting method, comprises the following steps:
[0046] 1. Clean the crucible, preheat it to 200-300°C, and spray paint; prepare various tools for smelting operation, clean it up, preheat it to 200-300°C, spray paint, and bake to remove moisture;
[0047] 2. Weigh the pre-prepared SR-1 refining and modifying refiner according to the needs of processing aluminum-silicon liquid, put it into the oven, bake at 200-300°C for 4-6 hours, set aside, SR-1 refining The metamorphic refiner consists of 10kg of NaNO 3 , 13kg of BaCl 2 , 10kg of NaF, 13kg of Na 3 AlF 6 , 21kg of K 2 TiF 6 、6kg of KBF 4 , 13kg of NaCl and 10kg of C powder.
[0048] 3. Furnace loading and melting: after spraying the coating on the crucible, the furnace can be loaded after the coating is dry. First, recycle materials are added, and then pure aluminum ingots are added. After the molten aluminum temperature reaches 700°C, pure silicon and aluminum are added. The silicon ratio ...
Embodiment 2
[0052] The process steps of the cast aluminum alloy smelting method in the second embodiment are basically the same as those in the first embodiment, except that the temperature for adding pure silicon to the molten aluminum is 700°C. SR-1 refining metamorphic refiner consists of 12kg of NaNO 3 , 15kg of BaCl 2 , 12kg of NaF, 15kg of Na 3 AlF 6 , 23kg of K 2 TiF 6 , 8kg of KBF 4 , 15kg of NaCl and 12kg of C powder. Add when the temperature of the aluminum-silicon liquid reaches 715° C., and the addition amount is 2.4% of the weight of the aluminum-silicon liquid.
Embodiment 3
[0054] The process steps of the casting aluminum alloy smelting method in the third embodiment are basically the same as those in the first embodiment, except that the temperature for adding pure silicon to the molten aluminum is 712°C. SR-1 refining metamorphic refiner consists of 14kg of NaNO 3 , 17kg of BaCl 2 , 14kg of NaF, 17kg of Na 3 AlF 6 , 25kg of K 2 TiF 6 , 10kg of KBF 4 , 17kg of NaCl and 14kg of C powder. Add when the temperature of the aluminum-silicon liquid reaches 715°C, and the amount added is 2.6% of the weight of the aluminum-silicon liquid.
PUM
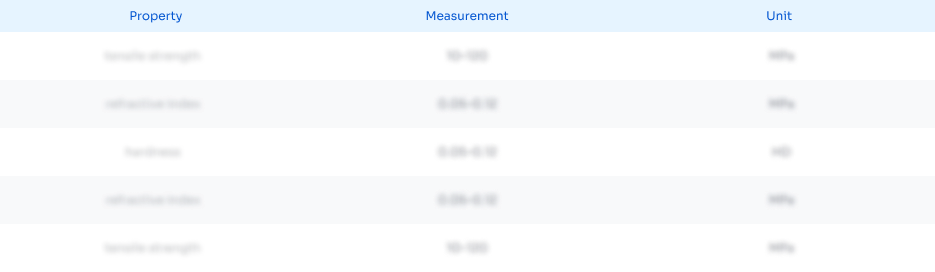
Abstract
Description
Claims
Application Information

- R&D Engineer
- R&D Manager
- IP Professional
- Industry Leading Data Capabilities
- Powerful AI technology
- Patent DNA Extraction
Browse by: Latest US Patents, China's latest patents, Technical Efficacy Thesaurus, Application Domain, Technology Topic, Popular Technical Reports.
© 2024 PatSnap. All rights reserved.Legal|Privacy policy|Modern Slavery Act Transparency Statement|Sitemap|About US| Contact US: help@patsnap.com