Flame length controllable high-efficient burner
A technology of flame length and burner, which is applied in the fields of gas-fired power generation, glass production, cement production, and metallurgy. It can solve problems such as insufficient power and strength, influence on co-combustion effect, and overall performance reduction of hot blast stoves, and achieve the extent of expanding distribution segregation , sufficient and rapid uniform mixing, worsening the effect of uniform distribution conditions
- Summary
- Abstract
- Description
- Claims
- Application Information
AI Technical Summary
Problems solved by technology
Method used
Image
Examples
Embodiment 1
[0032] Embodiment 1: There are 2 middle rings and 1 top ring, each middle ring has only one spout layer, and its 2 spout layers are closely adjacent.
[0033] The flame length controllable burner is made of refractory materials masonry or pouring, including the mixing pre-combustion chamber, the necking section, the middle inlet, the middle ring, and the middle nozzle. The gap between the mixing pre-combustion chamber and the final combustion chamber is In the necking section, the mixing pre-chamber is set in the central area of the middle ring, the middle inner side of the mixing pre-chamber is provided with a middle nozzle, the middle outer side of the mixing pre-chamber is provided with a middle inlet and a middle ring, the middle inlet, The middle ring, the middle nozzle, and the mixing pre-combustion chamber are connected to each other in turn; the middle ring is divided into two, which are divided into the middle ring of fuel gas medium and the middle ring of combustion...
Embodiment 2
[0034] Embodiment 2: 3 middle loops, 1 top loop, 4 spout layers in the middle of the burner; top-combustion hot blast stove, the burner is buckled upside down on the top of the hot blast stove (the burner outlet is facing down) and connected with Concentric application mode of hot blast stove.
[0035] like figure 1 , Figure 4 , Figure 5 , Image 6 As shown, the flame length controllable burner is made of refractory material masonry or pouring (refractory material annular masonry or pouring body 1), including mixing pre-combustion chamber 2, necking section 16, 3 middle inlets, 3 There are two middle rings, four middle nozzle layers, and a necking section 16 between the mixing pre-chamber 2 and the final combustion chamber 4; the mixing pre-chamber 2 is located in the central area of the three middle rings, and the mixing pre-chamber The inner side of the middle part is provided with a middle spout, and the outer middle part of the mixing pre-chamber is provided with a...
Embodiment 3
[0043] Embodiment 3: 3 middle loops, 1 top loop, 4 spout layers in the middle of the burner; top-combustion hot blast stove, the burner is buckled upside down on the top of the hot blast stove (the burner outlet is facing down) and connected with Concentric application mode of hot blast stove. Combustion air is used as the main adjustment means for flame length regulation.
[0044] like figure 2 As shown, its structure is basically the same as that of Embodiment 1, the difference is that the top ring road 19 is not connected with the first combustion air medium middle ring road 11, but the top ring road 19 is connected with the third combustion air medium sub-pipe 24 The third combustion-supporting air medium branch pipe 24 is connected with the combustion-supporting air medium main pipe 9 , and the third combustion-supporting air medium branch pipe 24 is respectively provided with a third regulating valve 25 and a first shut-off valve 26 .
PUM
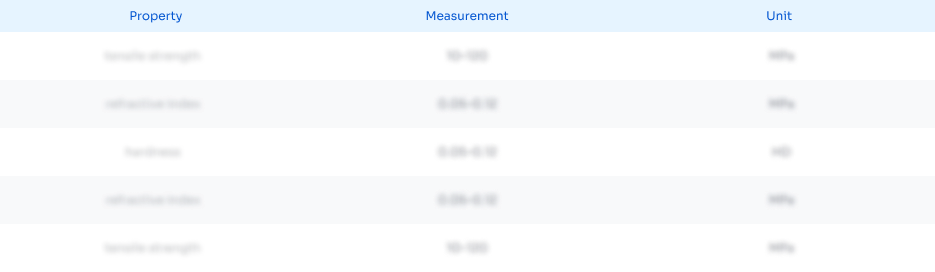
Abstract
Description
Claims
Application Information

- Generate Ideas
- Intellectual Property
- Life Sciences
- Materials
- Tech Scout
- Unparalleled Data Quality
- Higher Quality Content
- 60% Fewer Hallucinations
Browse by: Latest US Patents, China's latest patents, Technical Efficacy Thesaurus, Application Domain, Technology Topic, Popular Technical Reports.
© 2025 PatSnap. All rights reserved.Legal|Privacy policy|Modern Slavery Act Transparency Statement|Sitemap|About US| Contact US: help@patsnap.com