Method for manufacturing optical element
A manufacturing method and technology for optical components, applied in the directions of optical components, optics, manufacturing tools, etc., can solve the problems affecting the accuracy of the outer diameter, the inconsistency of the optical axis and the centering axis, etc., and achieve easy rough machining, cheap manufacturing, and shape reduction. the effect of the restriction
- Summary
- Abstract
- Description
- Claims
- Application Information
AI Technical Summary
Problems solved by technology
Method used
Image
Examples
Embodiment Construction
[0031] Hereinafter, embodiments of the present invention will be described in detail with reference to the drawings. FIG. 1 is a side view of a lens material 1 . FIG. 2 is a side view of the completed optical element 3 . The optical element 3 of this embodiment has optical function surfaces 10 and 10 on both surfaces, and a peripheral portion 11 is formed on the periphery thereof, and is formed by press working of glass. As shown in FIG. 1 , a lens material 1 called a protrusion which is preliminarily formed in an elliptical shape is prepared, heated and softened, and pressed with a die to form an optical element 3 shown in FIG. 2 .
[0032] The projection material 1 which is the lens material 1 can be formed into a predetermined shape by dropping an appropriate amount of glass material in a softened state from a glass melting furnace, changing the shape of the receiving part, and the like. In the present embodiment, the elliptical shape shown in FIG. 1 is shown, but other s...
PUM
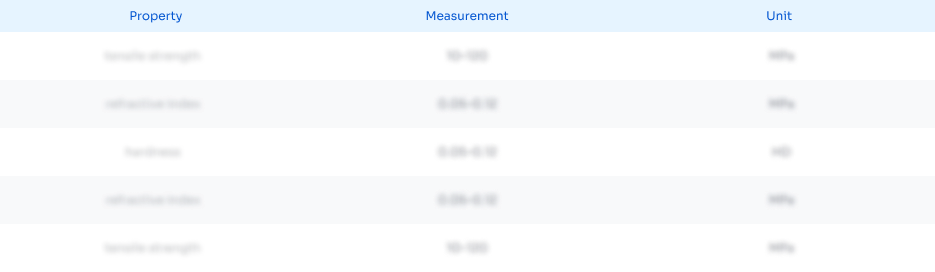
Abstract
Description
Claims
Application Information

- R&D Engineer
- R&D Manager
- IP Professional
- Industry Leading Data Capabilities
- Powerful AI technology
- Patent DNA Extraction
Browse by: Latest US Patents, China's latest patents, Technical Efficacy Thesaurus, Application Domain, Technology Topic, Popular Technical Reports.
© 2024 PatSnap. All rights reserved.Legal|Privacy policy|Modern Slavery Act Transparency Statement|Sitemap|About US| Contact US: help@patsnap.com