Semiconductor packer and production for godown chip
A package and semiconductor technology, which is applied to the field of stacked chip semiconductor packages and their manufacturing methods, can solve the problems of increasing the complexity of the overall packaging process, the required time course, the inconvenience of the process, and the increase in cost, so as to improve the heat dissipation efficiency. and electrical quality, reducing packaging costs and improving packaging efficiency
- Summary
- Abstract
- Description
- Claims
- Application Information
AI Technical Summary
Problems solved by technology
Method used
Image
Examples
Embodiment 1
[0036] The semiconductor package of the present invention includes: a chip carrier; a first chip 41 that is connected and electrically connected to the chip carrier; a heat sink 43 formed with a plurality of through openings, connected on the first chip 41 and not Contacting the chip carrier; connecting the second chip 42 on the heat sink, and the second chip 42 is electrically connected to the chip carrier through the wire passing through the opening 430 of the heat sink 43; and formed on the heat sink 43 The encapsulant 45 on the chip carrier covers the first chip 41 , the second chip 42 , the wires and the heat sink 43 . Wherein, the chip carrier is the substrate unit 40.
[0037] Please refer to FIG. 4A to FIG. 4H , which are process diagrams of Embodiment 1 of the stacked chip semiconductor package manufacturing method of the present invention.
[0038] As shown in Figures 4A and 4B, at first, a substrate module sheet 40A is provided, and the substrate module sheet 40A i...
Embodiment 2
[0047] Please refer to FIG. 6 , which is a schematic cross-sectional view of Embodiment 2 of a semiconductor package manufactured by referring to the method for manufacturing a semiconductor package with stacked chips of the present invention. The semiconductor package of the present invention is made by a method similar to that of Example 1. The difference is that in the semiconductor package of Example 2, when the second chip 52 is bonded, the heat dissipation is utilized. The component 53 serves as a ground plane, and electrically connects the second chip 52 to the heat sink 53 through the ground wire 540, so as to improve the electrical function of the semiconductor package. Wherein, in order to improve the connection effect of the grounding wire (gold wire) on the heat sink 53, the connection position of the wire is plated with silver on the heat sink 53 to improve bonding.
Embodiment 3
[0049]Please refer to FIG. 7 , which is a schematic cross-sectional view of Embodiment 3 of the semiconductor package structure manufactured by referring to the semiconductor package method for stacking chips of the present invention. The semiconductor package structure of the present invention is made by a method similar to that of the semiconductor structure of Example 1, the difference is that the chip carrier used in this example is an LGA (LAND GRID ARRAY) substrate 60, so that the first and The second chips 61 , 62 can be electrically connected to external devices via a plurality of metal contacts 60 a arranged on the bottom surface of the LGA substrate 60 .
PUM
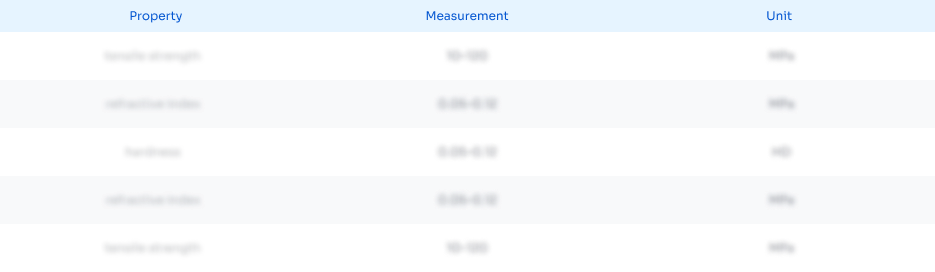
Abstract
Description
Claims
Application Information

- R&D
- Intellectual Property
- Life Sciences
- Materials
- Tech Scout
- Unparalleled Data Quality
- Higher Quality Content
- 60% Fewer Hallucinations
Browse by: Latest US Patents, China's latest patents, Technical Efficacy Thesaurus, Application Domain, Technology Topic, Popular Technical Reports.
© 2025 PatSnap. All rights reserved.Legal|Privacy policy|Modern Slavery Act Transparency Statement|Sitemap|About US| Contact US: help@patsnap.com