Architected material design for seismic isolation
a material design and seismic isolation technology, applied in the direction of shockproofing, bridges, mechanical equipment, etc., can solve the problems of limiting the maximum allowed lateral displacement, affecting the seismic isolation effect, and limiting the dimensions of the isolator
- Summary
- Abstract
- Description
- Claims
- Application Information
AI Technical Summary
Benefits of technology
Problems solved by technology
Method used
Image
Examples
examples
[0088]Numerical simulations are performed to assess the performance of the newly architected material. Because in the proposed cellular periodic material the mechanical properties (e.g., Young Modulus and Shear Modulus) of the unit cells' layers replicate on a large scale the properties of the unit cell, a numerical simulation of the unit cell was performed.
[0089]A finite element model of a particular embodiment of the single cell (embodiment FIG. 4a) is presented under a vertical pressure of 20 MPa and for lateral deflections resulting in shearing forces of 20%-30% of the structure weight. This load scenario may represent the behavior for Maximum Credible Earthquakes.
[0090]A parametric analysis based on the variation of some geometrical parameters of the unit cell is performed in order to show how the mechanical property of the architected material can be optimized by changing the geometry of unit cell.
[0091]A set of values for shells thickness (S1=0.1 mm, S2=0.2 mm, S3=0.4 mm), a ...
PUM
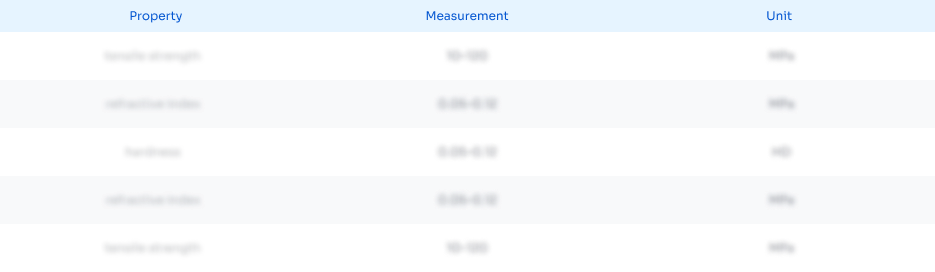
Abstract
Description
Claims
Application Information

- R&D
- Intellectual Property
- Life Sciences
- Materials
- Tech Scout
- Unparalleled Data Quality
- Higher Quality Content
- 60% Fewer Hallucinations
Browse by: Latest US Patents, China's latest patents, Technical Efficacy Thesaurus, Application Domain, Technology Topic, Popular Technical Reports.
© 2025 PatSnap. All rights reserved.Legal|Privacy policy|Modern Slavery Act Transparency Statement|Sitemap|About US| Contact US: help@patsnap.com