Method and system for process controlling of plants in an opc-ua based machine-to-machine network
a technology of machine-to-machine network and process control system, applied in the field of electronic process control, can solve the problems of inflexibility of plant control system, less flexible supervisory process control and manufacturing information system offerings, and inability to design process control installations, etc., to achieve the effect of reducing costs, simplifying integration into automation systems, and increasing up-to-date plant capacity
- Summary
- Abstract
- Description
- Claims
- Application Information
AI Technical Summary
Benefits of technology
Problems solved by technology
Method used
Image
Examples
Embodiment Construction
[0029]FIG. 1 illustrates, schematically, an architecture for a possible implementation of an embodiment of the inventive method and system for process controlling of plants and plant control systems in an OPC UA based Machine-to-Machine (M2M) network based on the inventive method. A plant 30 associated with a plant control system 20 includes a plurality of interlocked elements 32 of one or more operational unit 31 of the plant 30. For example taking roller mills, the operational units 31 can include rollers, motors to drives the hanger of the grinding rollers, treadmills, deflectors, gates, temperature or other parameter controls as measuring devices, interrupt devices etc. etc. The operational units 31 depend on the type of plant 30 and its specific technical realization, to which the plant control systems 20 and the adaptive process control system 10 should be applied. The interlocked elements 32 create the connection between operational units 31 and the I / O elements of the plant ...
PUM
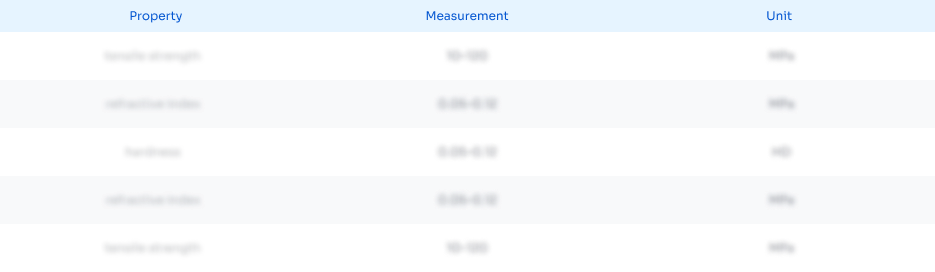
Abstract
Description
Claims
Application Information

- R&D
- Intellectual Property
- Life Sciences
- Materials
- Tech Scout
- Unparalleled Data Quality
- Higher Quality Content
- 60% Fewer Hallucinations
Browse by: Latest US Patents, China's latest patents, Technical Efficacy Thesaurus, Application Domain, Technology Topic, Popular Technical Reports.
© 2025 PatSnap. All rights reserved.Legal|Privacy policy|Modern Slavery Act Transparency Statement|Sitemap|About US| Contact US: help@patsnap.com