Bearing structure
- Summary
- Abstract
- Description
- Claims
- Application Information
AI Technical Summary
Benefits of technology
Problems solved by technology
Method used
Image
Examples
modification examples
[0092]One embodiment of the present invention was described above, but the present invention is not limited to this and can be modified as described below, for instance.
[0093]In the embodiment described above, a composition is described in which the constant-velocity joint 1 has a tripod configuration, but the form of the joint may be modified suitably. For example, the joint may be changed to a double-offset joint, a cross groove joint, or a fixed joint. Of these, if the constant-velocity joint 1 is a cross groove joint, then the sliding grooves of the outer ring are inclined in the round circumferential direction with respect to the axis line (axial direction), and the balls (sliding elements) of the trunnion assembly slide along the sliding grooves, in other words, in an oblique direction with respect to the axis line.
[0094]In the embodiment described above, a composition is explained in which drive force is input to the outer ring 10, but it is also possible to adopt a compositi...
PUM
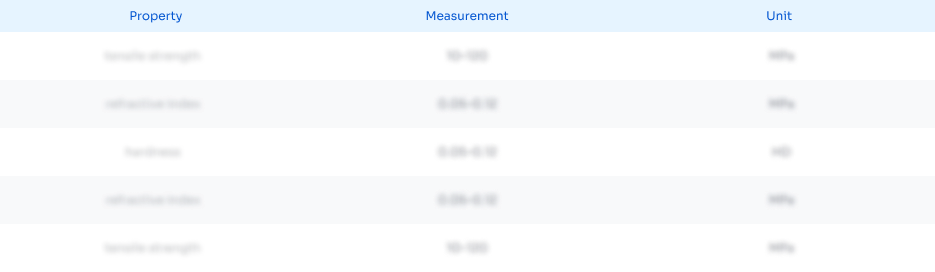
Abstract
Description
Claims
Application Information

- R&D
- Intellectual Property
- Life Sciences
- Materials
- Tech Scout
- Unparalleled Data Quality
- Higher Quality Content
- 60% Fewer Hallucinations
Browse by: Latest US Patents, China's latest patents, Technical Efficacy Thesaurus, Application Domain, Technology Topic, Popular Technical Reports.
© 2025 PatSnap. All rights reserved.Legal|Privacy policy|Modern Slavery Act Transparency Statement|Sitemap|About US| Contact US: help@patsnap.com