Transport unit
a technology of transport unit and telescopic carriage, which is applied in the direction of program-controlled manipulators, metal-working feeding devices, arms, etc., can solve the problems of complicated telescopic carriage arrangement and limited kinematics of this press transfer system, and achieve the effect of reducing the opening width requirement, low overall height, and fast and accurate movement of the gripping tool and the held workpi
- Summary
- Abstract
- Description
- Claims
- Application Information
AI Technical Summary
Benefits of technology
Problems solved by technology
Method used
Image
Examples
first embodiment
[0056]In FIG. 2, the transmission means (19) is designed as a rack-and-pinion drive, whereby motor (18) drives a pinion directly or via an upstream gear, which pinion meshes with a rack aligned along the support bar (11) and arranged on the top side of same. The second variant of FIG. 3 may also have such a rack-and-pinion drive or a different drive, which converts the motor rotation into a translatory movement of the support bar (11).
third embodiment
[0057]In FIGS. 4 through 10, the transmission means (19) is designed as a belt drive, whereby a pinion associated with the motor (18) meshes with a toothed belt in an omega loop that is finite and fixed with both ends at the front areas of the support bar (11). The belt drive (19) is arranged, e.g., on the top side and at a longitudinal edge of the support bar (11).
[0058]There are likewise various embodiments for the pivot drive (26). It is used to influence the rotary or pivoting position of the tool holder (16) at its carriage (13), whereby this is uniformly possible in all carriage positions.
[0059]The pivot drive (26) may likewise have a controllable motor (27). As in the feed drive (17), this may be an electric motor, especially an electric servomotor, which is likewise connected to the robot control system and makes possible a fast and exact workpiece rotation and a positioning and holding of the rotary position as well. The holding forces can be applied by the motors (18, 27) ...
PUM
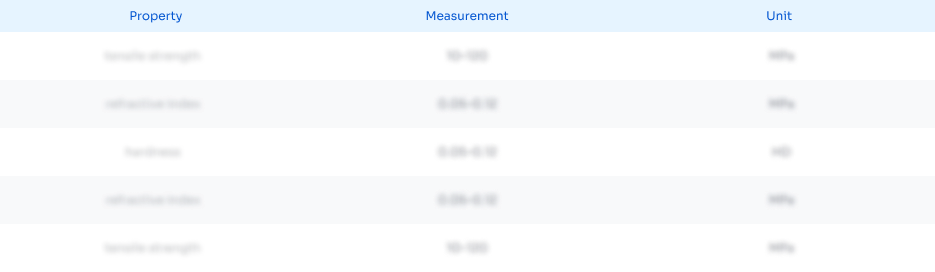
Abstract
Description
Claims
Application Information

- R&D
- Intellectual Property
- Life Sciences
- Materials
- Tech Scout
- Unparalleled Data Quality
- Higher Quality Content
- 60% Fewer Hallucinations
Browse by: Latest US Patents, China's latest patents, Technical Efficacy Thesaurus, Application Domain, Technology Topic, Popular Technical Reports.
© 2025 PatSnap. All rights reserved.Legal|Privacy policy|Modern Slavery Act Transparency Statement|Sitemap|About US| Contact US: help@patsnap.com