Pressure control valve arrangement having an eccentrically mounted double magnet
a technology of eccentric mounting and pressure control valve, which is applied in the direction of diaphragm valve, valve details, braking systems, etc., can solve the problems of reducing the effective flow diameter and entail additional costs for producing and mounting the reducing sleeves, so as to achieve the effect of simple manufacturing and assembly and more cost-effectiveness
- Summary
- Abstract
- Description
- Claims
- Application Information
AI Technical Summary
Benefits of technology
Problems solved by technology
Method used
Image
Examples
Embodiment Construction
[0029]According to FIG. 1, a vehicle equipped with an ABS brake system has a front axle 1 and a rear axle 2. Wheels 3a and 3b are arranged on the front axle 1; the rear axle 2 has, for example, wheels 4a and 4b in each case equipped with twin tires. The ABS brake system serving for braking these wheels 3a, 3b and 4a, 4b is designed here in the manner of a 4S / 4C system (four sensors, four channels). This means that, overall, four rotational speed sensors 5a-5d and four pressure control valve arrangements 7a-7d are available here. The pressure control valve arrangements 7a-7d serve for the activation of respectively assigned brake cylinders 6a-6d. All the pressure control valve arrangements 7a-7d are connected to a foot-operated brake valve 9 via a branching pneumatic brake pressure line 8.
[0030]The driver, when actuating the foot-operated brake valve 9, generates a brake pressure which, passing through the pressure control valve arrangements 7a-7d, is transferred by the pneumatic bra...
PUM
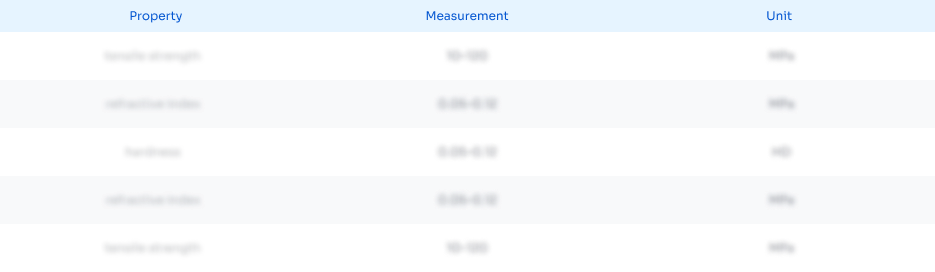
Abstract
Description
Claims
Application Information

- R&D
- Intellectual Property
- Life Sciences
- Materials
- Tech Scout
- Unparalleled Data Quality
- Higher Quality Content
- 60% Fewer Hallucinations
Browse by: Latest US Patents, China's latest patents, Technical Efficacy Thesaurus, Application Domain, Technology Topic, Popular Technical Reports.
© 2025 PatSnap. All rights reserved.Legal|Privacy policy|Modern Slavery Act Transparency Statement|Sitemap|About US| Contact US: help@patsnap.com