Vessel with active mechanism for controlled towing
a technology of towing mechanism and towed body, which is applied in the field of towing sensors on ships with active mechanisms, can solve the problems of increased force on the towed body, increased safety hazards, and difficulty in controlling small vessels used to tow sensors, so as to reduce deleterious effects, improve safety, and improve safety. the effect of safety
- Summary
- Abstract
- Description
- Claims
- Application Information
AI Technical Summary
Benefits of technology
Problems solved by technology
Method used
Image
Examples
Embodiment Construction
[0014]Referring now to the drawings and particularly to FIGS. 1-3, it can be seen that a vessel with an active mechanism and a controlled towing system is designated generally by the numeral 10. The system 10 includes a vessel 12 which may be any kind of water-borne craft. In most embodiments of the present invention the craft is a relatively small motorized craft, but the concepts of the present invention can be employed with any type of towing vessel. The vessel 12 carries a vessel position and motion sensor 14 which monitors the position speed, pitch, yaw, roll and other operational characteristics of the vessel. The data collected by the sensor 14 is transmitted via a data line 16. In some embodiments the sensor 14 may wirelessly transmit data associated with or collected by the sensor 14. The vessel 12 includes a cabin 18 which houses various instruments and control systems for operating the vessel 12. In some embodiments the cabin may accommodate personnel and in other embodim...
PUM
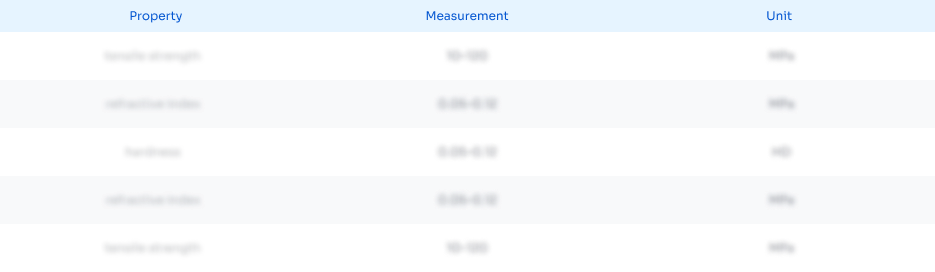
Abstract
Description
Claims
Application Information

- R&D
- Intellectual Property
- Life Sciences
- Materials
- Tech Scout
- Unparalleled Data Quality
- Higher Quality Content
- 60% Fewer Hallucinations
Browse by: Latest US Patents, China's latest patents, Technical Efficacy Thesaurus, Application Domain, Technology Topic, Popular Technical Reports.
© 2025 PatSnap. All rights reserved.Legal|Privacy policy|Modern Slavery Act Transparency Statement|Sitemap|About US| Contact US: help@patsnap.com