System for combined cycle mechanical drive in cryogenic liquefaction processes
a technology of combined cycle and mechanical drive, which is applied in the direction of refrigeration and liquifaction, lighting and heating equipment, solidification, etc., to achieve the effect of low fuel demand and low operating cos
- Summary
- Abstract
- Description
- Claims
- Application Information
AI Technical Summary
Benefits of technology
Problems solved by technology
Method used
Image
Examples
Embodiment Construction
[0014]As illustrated in FIG. 1, the present refrigeration assembly comprises three different refrigeration loops:[0015]a high temperature loop, here depicted with two compressors 12, 13 or compressor stages and one expander 1 or expander stage, hereinafter only denoted compressors and expanders, respectively. As for all three loops this is a base case, but if the process advantages are obvious, this lay out may consist of a different number of compressor or expander units, depending process requirements or other criteria. The high temperature loop is used for de-superheating;[0016]a medium temperature loop is used to condense the LNG, and this loop normally consists of two compressors 14, 15 and one expander 2; and[0017]a low temperature loop consists of three compressors 16, 17, 18 and one expander in the base case also, and is used to sub-cool the LNG.
[0018]Further information for the refrigeration assembly is to be found in the Norwegian Patent Application 2008 3740 and the same ...
PUM
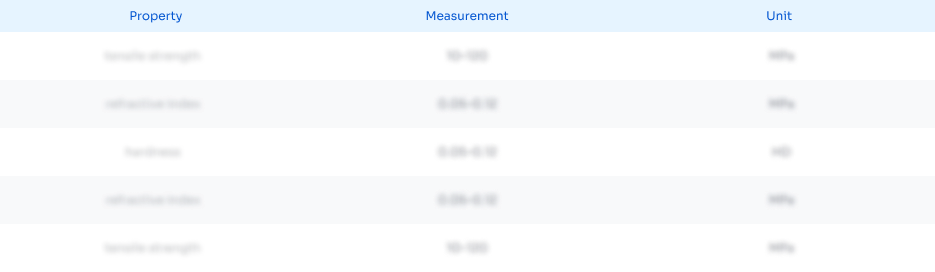
Abstract
Description
Claims
Application Information

- R&D
- Intellectual Property
- Life Sciences
- Materials
- Tech Scout
- Unparalleled Data Quality
- Higher Quality Content
- 60% Fewer Hallucinations
Browse by: Latest US Patents, China's latest patents, Technical Efficacy Thesaurus, Application Domain, Technology Topic, Popular Technical Reports.
© 2025 PatSnap. All rights reserved.Legal|Privacy policy|Modern Slavery Act Transparency Statement|Sitemap|About US| Contact US: help@patsnap.com