Process for obtaining treated coal and silica from coal containing fly ash
- Summary
- Abstract
- Description
- Claims
- Application Information
AI Technical Summary
Benefits of technology
Problems solved by technology
Method used
Image
Examples
Embodiment Construction
[0014]As noted above, the present invention provides for an efficient separation of metal and inorganic constituents of coal fly ash while also providing the almost complete recovery of commercial-grade silica present in the fly ash. The method reduces the unwanted fly ash constituents (such as metal oxides, sulfur and silicon dioxide) to an impurity level that easily meets current environmental control regulations without requiring complex and expensive emission control equipment, particularly in coal-fired turbine plants, power stations and the like. At the same time, the method provides an economical process for recovering essentially pure silica as a valuable byproduct.
[0015]An exemplary process according to the invention isolates metal “impurities” present in the fly ash by converting the components to soluble mineral oxides that can be removed as waste from the system. The process also reforms, and then segregates, the silica component for removal as a separate product. As a r...
PUM
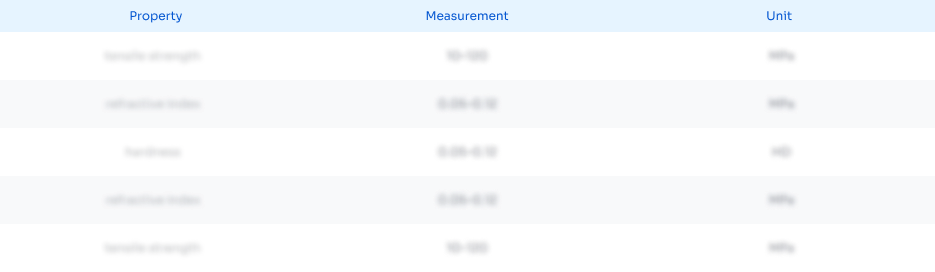
Abstract
Description
Claims
Application Information

- R&D
- Intellectual Property
- Life Sciences
- Materials
- Tech Scout
- Unparalleled Data Quality
- Higher Quality Content
- 60% Fewer Hallucinations
Browse by: Latest US Patents, China's latest patents, Technical Efficacy Thesaurus, Application Domain, Technology Topic, Popular Technical Reports.
© 2025 PatSnap. All rights reserved.Legal|Privacy policy|Modern Slavery Act Transparency Statement|Sitemap|About US| Contact US: help@patsnap.com