Refrigeration system
a refrigeration system and high-pressure technology, applied in the field of refrigeration systems, can solve the problems of limited possibility of accumulation of refrigerant on the high-pressure side, lack of refrigerating capacity, and inability to meet the needs of larger-scale distributed systems, etc., to achieve novel valve control, high pressure, and loss of heat transfer performance
- Summary
- Abstract
- Description
- Claims
- Application Information
AI Technical Summary
Benefits of technology
Problems solved by technology
Method used
Image
Examples
Embodiment Construction
[0025]One embodiment of the invention is illustrated schematically in FIG. 1.
[0026]In this system the refrigerant carbon dioxide is used for cooling of chilled food display cases in a supermarket. A set of one or more compressors (1A, 1B etc) pump refrigerant gas to a high pressure condition at which it can reject heat to atmosphere or some other cooling medium. The gas is conducted from the compressor(s) through pipes (6B, 6C) to a heat rejection device (2). From the heat rejection device the cooled refrigerant passes through pipes (6D, 6F) to a heat exchanger located in the receiver (4) and from there through pipes (6G) to a set of one or more system evaporators (5A, 5B etc).
[0027]When the temperature of the heat sink (the zone to which heat is rejected from heat rejection device (2)) is higher than approximately 25° C. then the compressors will be required to raise the carbon dioxide gas to a supercritical pressure, typically in the range 80 to 120 bar absolute. This can be descr...
PUM
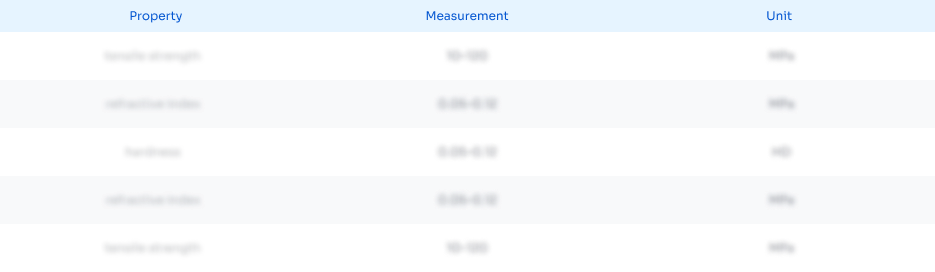
Abstract
Description
Claims
Application Information

- R&D
- Intellectual Property
- Life Sciences
- Materials
- Tech Scout
- Unparalleled Data Quality
- Higher Quality Content
- 60% Fewer Hallucinations
Browse by: Latest US Patents, China's latest patents, Technical Efficacy Thesaurus, Application Domain, Technology Topic, Popular Technical Reports.
© 2025 PatSnap. All rights reserved.Legal|Privacy policy|Modern Slavery Act Transparency Statement|Sitemap|About US| Contact US: help@patsnap.com