ZnO BASED SEMICONDUCTOR LIGHT EMITTING DEVICE AND ITS MANUFACTURE METHOD
- Summary
- Abstract
- Description
- Claims
- Application Information
AI Technical Summary
Benefits of technology
Problems solved by technology
Method used
Image
Examples
first embodiment
[0041]Evaluation results by the above-described method indicated that the ZnO1-xSx layer of the first embodiment had an S composition x of 0.1, a band gap energy was 2.93 eV, a surface roughness Ra was 1.0 nm, and an ionizing potential was 5.3 eV. An RHEED image of the ZnO1-xSx layer of the thin sample had a streak pattern. The ZnO1-xSx layer having good crystallinity and flatness was obtained.
[0042]Next, the second comparative example will be described. A ZnO1-xSx layer was grown to a thickness of 100 nm by the method similar to the first embodiment. As different from the first embodiment, annealing was not performed after the film was formed.
[0043]A surface roughness was measured with AFM, and RHEED measurements were conducted during growth. The ZnO1-xSx layer of the second comparative example had a surface roughness Ra of 1.09 nm, and the RHEED image indicated a streak pattern. Since an S concentration is low, it can be considered that a film having relatively good crystallinity ...
seventh embodiment
[0101]After these electrodes are formed, an electrode alloying process is performed, for example, in an oxygen atmosphere at 400° C. to 800° C. An alloying process time is, for example, one minute to ten minutes. In this manner, the light emitting device of the seventh embodiment is manufactured. Although the ZnO substrate having n-type conductivity is used as the substrate 8, an SiC substrate and a GaN substrate having n-type conductivity may also be used.
[0102]Next, with reference to FIG. 10, description will be made on a manufacture method for a light emitting device of the eighth embodiment. Different points from the seventh embodiment reside in that an insulating sapphire substrate 8a is used and therefore an electrode forming process is changed.
[0103]Similar to the seventh embodiment, layers from an n-type ZnO buffer layer 20 to a p-type ZnO layer 23 are formed on the substrate 8a. After the wafer formed with the layers up to the p-type ZnO layer 23 is dismounted from the film...
eighth embodiment
[0107]In the light emitting device of the eighth embodiment, the insulating sapphire substrate can be used. A ZnO substrate, an SiC substrate or a GaN substrate may also be used.
[0108]In the above-described embodiments, the c-plane ZnO substrate is used and the semiconductor device is formed on the + c-plane by way of example. The semiconductor device may be formed on the − c-plane. The semiconductor device may be formed also on the ZnO substrate having the a-plane or an m-plane.
[0109]As described above, setting 0.251-xSx layer is sandwiched between ZnO layers, carriers can be confined in the ZnO1-xSx layer. It is therefore expected for example that a blue light emitting device having a high emission efficiency can be manufactured. By performing annealing at 500° C. or higher, and lower than 1000° C. after the ZnO1-xSx layer is formed, flatness of the ZnO1-xSx layer can be improved.
[0110]As studies have been made with reference to FIG. 4, the structure that the ZnO1-xSx layer is san...
PUM
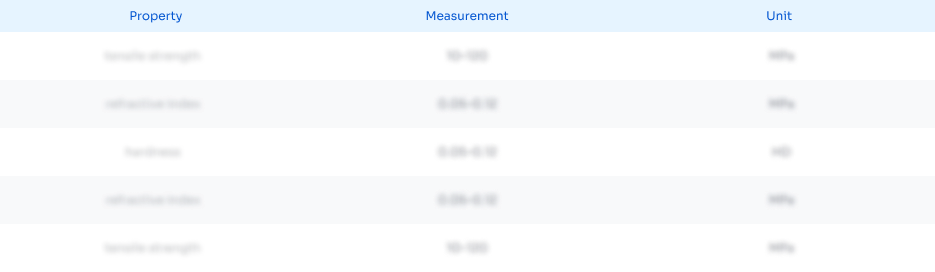
Abstract
Description
Claims
Application Information

- R&D
- Intellectual Property
- Life Sciences
- Materials
- Tech Scout
- Unparalleled Data Quality
- Higher Quality Content
- 60% Fewer Hallucinations
Browse by: Latest US Patents, China's latest patents, Technical Efficacy Thesaurus, Application Domain, Technology Topic, Popular Technical Reports.
© 2025 PatSnap. All rights reserved.Legal|Privacy policy|Modern Slavery Act Transparency Statement|Sitemap|About US| Contact US: help@patsnap.com