Ultra-low temperature freezer, refrigeration system and vacuum apparatus
a vacuum apparatus and freezer technology, applied in the field of ultra-low temperature freezers, refrigeration systems and vacuum devices, can solve the problems of reducing the flow rate of liquid refrigerant obtained by gas refrigerant liquefaction of the supercooler, and affecting the cooling efficiency of the main cooler. , to achieve the effect of shortening the cool-down time, simple structure and enhancing the cooling efficiency of the main cooler
- Summary
- Abstract
- Description
- Claims
- Application Information
AI Technical Summary
Benefits of technology
Problems solved by technology
Method used
Image
Examples
embodiment 1
[0178]FIG. 1 shows an example of the layout of a vacuum deposition apparatus A serving as a vacuum apparatus according to an embodiment of the invention. Reference numeral 100 denotes a vacuum chamber in which films are deposited on unshown substrates (also referred to as wafers) with the inside kept under vacuum. The vacuum chamber 100 has a carry-in-and-out opening (not shown) that can be opened and closed by an opening and closing door 101. Substrates on which films are to be deposited are carried in the vacuum chamber 100 or the substrates on which films have been deposited are carried out of it, in each case with the opening and closing door 101 open. The vacuum chamber 100 is connected through a communicating passage 102 with a vacuum pump 103. A gate valve 104 is disposed at the connecting point of the communicating passage 102 and the vacuum chamber 100 to switch between providing flow communication between them and interrupting the flow communication of them by turning the ...
embodiment 2
[0205]FIG. 6 shows Embodiment 2 of the invention (where the same parts as in FIGS. 1 to 5 in this and following embodiments are identified by the same reference characters and a detailed description thereof is not given). In Embodiment 1, the flow rate of liquid refrigerant into the secondary side 31b of the supercooler 31 is kept higher than that into the cryocoil 32 by setting the height of the sub refrigerant circuit 39 to be lower than that of the main refrigerant circuit 38. In contrast, in this embodiment, the sub refrigerant circuit 39 and the main refrigerant circuit 38 are located at the same height but the sub refrigerant circuit 39 has a larger cross sectional area than the main refrigerant circuit 38.
[0206]More specifically, in this embodiment, in contrast to Embodiment 1, the collecting portion 35a and main branch portion 35b of the branch pipe 35, the main refrigerant pipe 2a connected to these portions, the sub-branch portion 35c of the branch pipe 35, and the sub ref...
embodiment 4
[0217]FIG. 9 shows the overall configuration of an ultra-low temperature freezer R according to Embodiment 4 of the invention. In the following Embodiments 4 to 13, the structure of the branch pipe 35 described in Embodiments 1 to 3 is not essential.
[0218]Embodiment 4 is characterized by the configuration of the defrosting circuit 45. Specifically, as shown in FIG. 9, a second oil separator 50 for separating refrigerator oil, such as lubrication oil for a compressor, from gas refrigerant is disposed between the upstream end of the defrosting circuit 45 and the solenoid shut-off valve 46 (and the oil separator 5 connected to the discharge part of the compressor 4 is referred to as a first oil separator). The refrigerator oil separated by the second oil separator 50 is returned, as with the first oil separator 5, through the oil return pipe 6 to the suction side of the compressor 4. The second oil separator 50 is disposed at a location along the defrosting circuit 45 at which the dist...
PUM
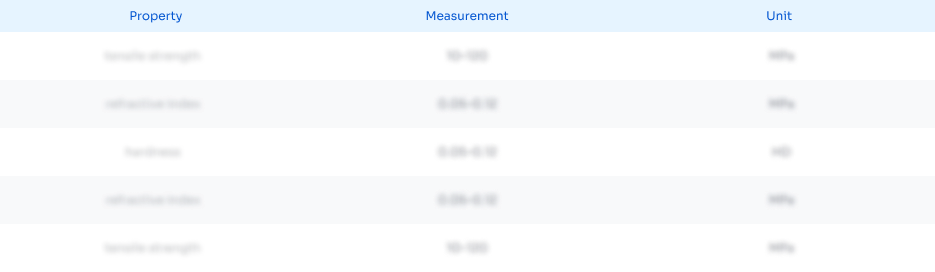
Abstract
Description
Claims
Application Information

- R&D
- Intellectual Property
- Life Sciences
- Materials
- Tech Scout
- Unparalleled Data Quality
- Higher Quality Content
- 60% Fewer Hallucinations
Browse by: Latest US Patents, China's latest patents, Technical Efficacy Thesaurus, Application Domain, Technology Topic, Popular Technical Reports.
© 2025 PatSnap. All rights reserved.Legal|Privacy policy|Modern Slavery Act Transparency Statement|Sitemap|About US| Contact US: help@patsnap.com