Screw pump rotor and method of reducing slip flow
- Summary
- Abstract
- Description
- Claims
- Application Information
AI Technical Summary
Benefits of technology
Problems solved by technology
Method used
Image
Examples
Embodiment Construction
[0024]Referring now to the drawings, wherein like reference numerals designate identical or corresponding parts throughout the several views, several embodiments of the pump rotor according to the disclosed invention will be described. One of the advantageous aspects of the disclosed invention is the use of a rotating inter-stage ring or brush seal to minimize and / or eliminate pump slip flow, thus providing for higher pressure rise per stage while being compliant to accommodate rotor deflections.
[0025]FIGS. 3-5 illustrate, respectively, a cross section view of a rotor 40, a cross sectional view of one tip of the screw threads of FIG. 3, and a ring seal 60 in accordance with an embodiment of the disclosed invention. Throughout this disclosure, the terms “ring seal,”“piston-ring seal,”“brush seal,”“inter-stage seal,”“split-ring seal,” or “seal” will be used interchangeably. As shown in FIG. 3, the rotor 40 includes a shaft 42, on the periphery of which a plurality of screw threads 44 ...
PUM
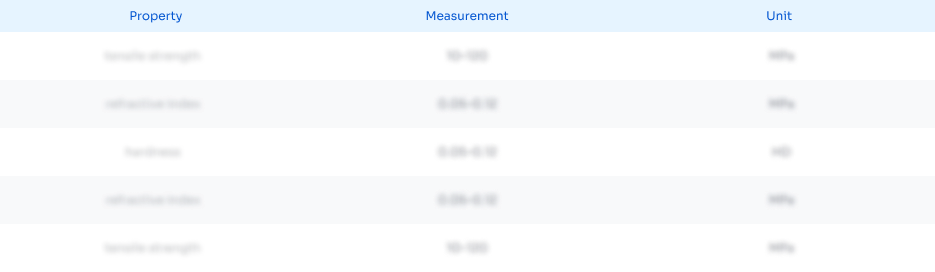
Abstract
Description
Claims
Application Information

- R&D
- Intellectual Property
- Life Sciences
- Materials
- Tech Scout
- Unparalleled Data Quality
- Higher Quality Content
- 60% Fewer Hallucinations
Browse by: Latest US Patents, China's latest patents, Technical Efficacy Thesaurus, Application Domain, Technology Topic, Popular Technical Reports.
© 2025 PatSnap. All rights reserved.Legal|Privacy policy|Modern Slavery Act Transparency Statement|Sitemap|About US| Contact US: help@patsnap.com