Reducing heat transfer surface area requirements of direct fired heaters without decreasing run length
a technology of heat transfer surface area and direct firing heater, which is applied in the direction of furnace-tube steam boilers, cracking processes, lighting and heating equipment, etc., can solve the problem of limiting the recirculation of combustion products in the firebox, and achieve the effect of reducing the size and cost of the heater
- Summary
- Abstract
- Description
- Claims
- Application Information
AI Technical Summary
Benefits of technology
Problems solved by technology
Method used
Image
Examples
Embodiment Construction
[0024]One embodiment of the invention, a delayed coking heater, as shown in FIG. 1, consisting of component parts as follows:[0025]1. A stack allowing for products of combustion leaving the convection section to be discharged to the atmosphere.[0026]2. Radiant section process heating coil outlet.[0027]3. Radiant section process heating coil outlet tubes.[0028]4. 180 degree return bends connecting adjacent horizontal tubes of radiant section process heating coils.[0029]5. Refractory lined walls of radiant section enclosure.[0030]6. Horizontal tubes of radiant section process heating coil.[0031]7. Radiant section process heating coil inlet connection.[0032]8. Radiant section process heating coil inlet tubes.[0033]9. Two rows of burners firing gaseous fuels.[0034]10. Horizontal tube auxiliary convection section heating coil inlet connection.[0035]11. Horizontal tube auxiliary convection section heating coil outlet connection.[0036]12. Horizontal tube process convection section pre-heat...
PUM
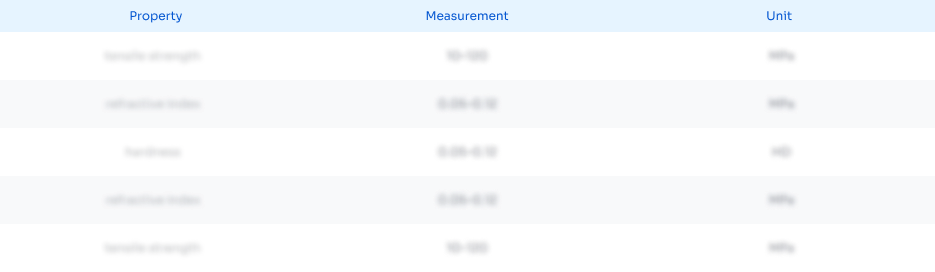
Abstract
Description
Claims
Application Information

- R&D
- Intellectual Property
- Life Sciences
- Materials
- Tech Scout
- Unparalleled Data Quality
- Higher Quality Content
- 60% Fewer Hallucinations
Browse by: Latest US Patents, China's latest patents, Technical Efficacy Thesaurus, Application Domain, Technology Topic, Popular Technical Reports.
© 2025 PatSnap. All rights reserved.Legal|Privacy policy|Modern Slavery Act Transparency Statement|Sitemap|About US| Contact US: help@patsnap.com