Method and system for reducing pollutant emissions of a power system
- Summary
- Abstract
- Description
- Claims
- Application Information
AI Technical Summary
Benefits of technology
Problems solved by technology
Method used
Image
Examples
Embodiment Construction
[0019]FIG. 1 provides a pictorial representation of an exemplary machine 5 having multiple systems and components that may cooperate to accomplish a task. Machine 5 may include a system for reducing pollutant emissions. Machine 5 may embody a fixed or mobile machine that performs some type of operation associated with an industry such as mining, construction, farming, transportation, or any other industry known in the art. For example, machine 5 may be an earth moving machine such as an excavator, a dozer, a loader, a backhoe, a motor grader, a dump truck, or any other earth moving machine. Additionally, machine 5 may include on-highway vehicles such as tractors, passenger cars, heavy and light trucks, and other similar vehicles. Machine 5 may include a first power source 18, a second power source 46, auxiliary devices 48, and an input member 16 connecting a transmission assembly 10 to power source 18 via a torque converter 19. Machine 5 may also include a frame 14 and an output mem...
PUM
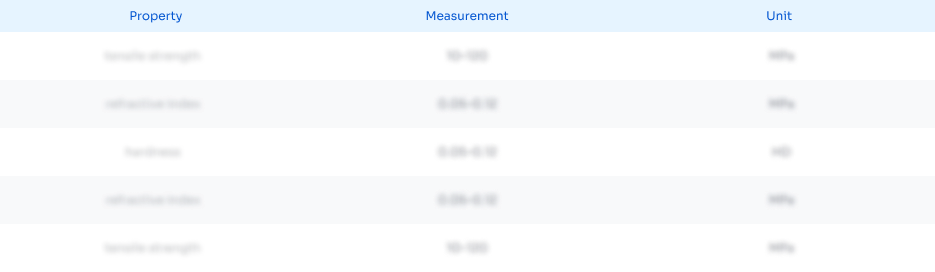
Abstract
Description
Claims
Application Information

- R&D
- Intellectual Property
- Life Sciences
- Materials
- Tech Scout
- Unparalleled Data Quality
- Higher Quality Content
- 60% Fewer Hallucinations
Browse by: Latest US Patents, China's latest patents, Technical Efficacy Thesaurus, Application Domain, Technology Topic, Popular Technical Reports.
© 2025 PatSnap. All rights reserved.Legal|Privacy policy|Modern Slavery Act Transparency Statement|Sitemap|About US| Contact US: help@patsnap.com