Wall Forms for Spraying Insulation
a technology of spraying foam insulation and wall forms, which is applied in the direction of walls, construction, building materials handling, etc., can solve the problems of complicated spraying foam insulation process, and achieve the effect of reducing trimming and was
- Summary
- Abstract
- Description
- Claims
- Application Information
AI Technical Summary
Benefits of technology
Problems solved by technology
Method used
Image
Examples
Embodiment Construction
[0022] The following description of the preferred embodiment(s) is merely exemplary in nature and is in no way intended to limit the invention, its application, or uses.
[0023] In FIG. 1, a panel shown generally at 10 is provided. Preferably, the panel has a width that corresponds to standard widths between studs, namely, 12, 18, 24 32 and 48 inches.
[0024] Panel 10 comprises a panel frame 14. Panel frame 14 is preferably made from flat aluminum or metal strips. Between the strips of panel frame 14, a mesh 16 is provided. Panel 10 is preferably provided with handle 18 for ease of handling. Preferably, panel 10 may be 96 inches in length, although it is recognized that panel length will vary according to need.
[0025] It will be appreciated that panel 10, for practical reasons, will come in various standard lengths. These lengths may be cumbersome for storage and transportation. Accordingly, these panels may be provided with means for combining multiple sections together. In the prese...
PUM
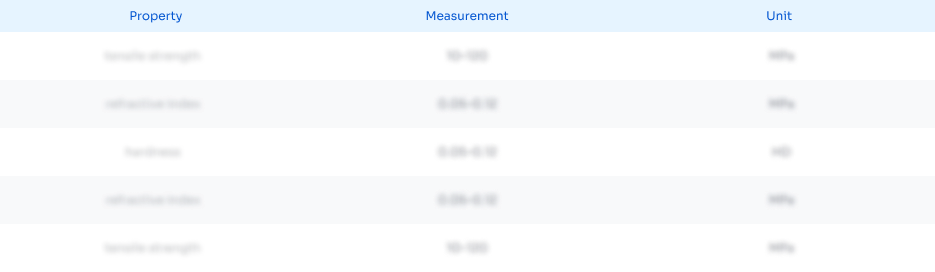
Abstract
Description
Claims
Application Information

- R&D
- Intellectual Property
- Life Sciences
- Materials
- Tech Scout
- Unparalleled Data Quality
- Higher Quality Content
- 60% Fewer Hallucinations
Browse by: Latest US Patents, China's latest patents, Technical Efficacy Thesaurus, Application Domain, Technology Topic, Popular Technical Reports.
© 2025 PatSnap. All rights reserved.Legal|Privacy policy|Modern Slavery Act Transparency Statement|Sitemap|About US| Contact US: help@patsnap.com