Non-feedback type load current controller
a load current controller and non-feedback technology, applied in the direction of instruments, heat measurement, digital computer details, etc., can solve the problems of excessive stress applied to the opening/closing element, abnormality sign cannot be detected, electric load operating in an unintentional state, etc., to achieve enhanced safety
- Summary
- Abstract
- Description
- Claims
- Application Information
AI Technical Summary
Benefits of technology
Problems solved by technology
Method used
Image
Examples
first embodiment
[0031]FIG. 1 is a block diagram showing the construction of a non-feedback type load current controller according to a first embodiment of the present invention.
[0032] In FIG. 1, reference numeral 100A represents a non-feedback type load current controller according to the first embodiment, and the non-feedback type load current controller 100A constitutes a controller for an automatic transmission for a vehicle, for example. Power is supplied from a driving power source 101 as an in-vehicle mount battery through a power supply switch 102 such as a key switch or the like.
[0033] The non-feedback type load current controller 100A is supplied with signals from an accelerator position sensor (APS) 103 for detecting the tread degree of an accelerator pedal (not shown), a vehicle speed sensor 104, a selector switch 105 for detecting the selected position of a selector lever, a temperature sensor (for example, oil temperature sensor) 112 for detecting the temperature of lubricating oil o...
second embodiment
[0140]FIG. 5 shows the construction of a non-feedback type load current controller according to a second embodiment of the present invention.
[0141] In FIG. 5, reference numeral 100B represents the non-feedback type load current controller according to the second embodiment, and as in the case of the first embodiment, the non-feedback type load current controller 100B according to the second embodiment is externally connected to a driving power source 101, a power source switch 102, an acceleration position sensor 103, a vehicle speed sensor 104, a selector switch 105, a temperature sensor 112 of a multistage automatic transmission 110, electrical loads 111a, 111b, . . . , 111n as electromagnetic solenoids, and an alarm display unit 106.
[0142] The difference of the second embodiment from the non-feedback type load current controller 100A of the first embodiment shown in FIG. 1 will be mainly described.
[0143] In FIG. 5, as in the case of the first embodiment, as the internal constr...
PUM
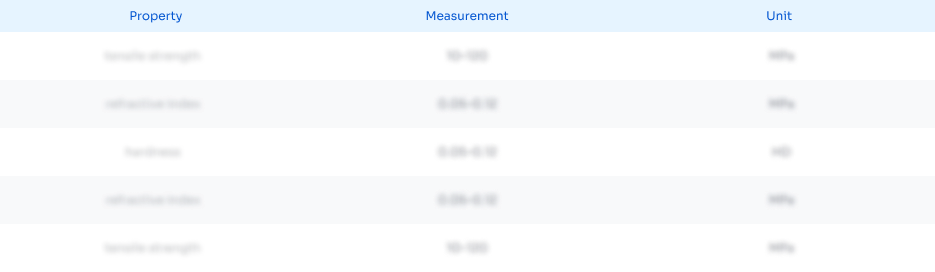
Abstract
Description
Claims
Application Information

- R&D
- Intellectual Property
- Life Sciences
- Materials
- Tech Scout
- Unparalleled Data Quality
- Higher Quality Content
- 60% Fewer Hallucinations
Browse by: Latest US Patents, China's latest patents, Technical Efficacy Thesaurus, Application Domain, Technology Topic, Popular Technical Reports.
© 2025 PatSnap. All rights reserved.Legal|Privacy policy|Modern Slavery Act Transparency Statement|Sitemap|About US| Contact US: help@patsnap.com