Thermal power plant
- Summary
- Abstract
- Description
- Claims
- Application Information
AI Technical Summary
Benefits of technology
Problems solved by technology
Method used
Image
Examples
Embodiment Construction
[0017] A preferred embodiment of the thermal power plant according to the present invention is shown in FIG. 1. The power plant comprises three turbines, namely a high pressure turbine 1, a medium pressure turbine 2 and a low pressure turbine 3, which are all mounted on a single drive shaft 21 connected to an electric generator 5. The turbines are operated by a water-steam-loop 4. The high pressure turbine 1 is supplied with highly pressurized hot steam from a steam raising unit 19. The steam expands to a certain extent in the high pressure turbine 1 and thereby causes the turbine and therewith the drive shaft 21 to rotate. The expanded steam exiting the high pressure turbine 1 is both of reduced pressure and of reduced temperature. Some of this steam is then diverted to a high-pressure pre-heater 18 arranged prior to the steam raising unit 19 in the water-steam-loop 4. The remaining portion of the steam is routed to a re-heater 20 from where it is forwarded to the medium-pressure t...
PUM
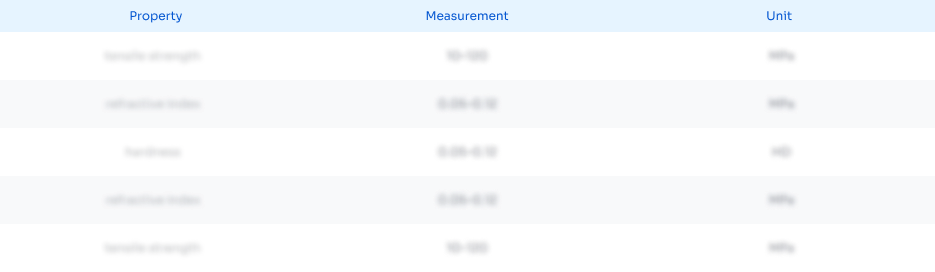
Abstract
Description
Claims
Application Information

- R&D
- Intellectual Property
- Life Sciences
- Materials
- Tech Scout
- Unparalleled Data Quality
- Higher Quality Content
- 60% Fewer Hallucinations
Browse by: Latest US Patents, China's latest patents, Technical Efficacy Thesaurus, Application Domain, Technology Topic, Popular Technical Reports.
© 2025 PatSnap. All rights reserved.Legal|Privacy policy|Modern Slavery Act Transparency Statement|Sitemap|About US| Contact US: help@patsnap.com