Systems and methods for modular instrument design and fabrication
a modular instrument and design technology, applied in the direction of girders, mounting boards, electrical apparatus construction details, etc., can solve the problems of reducing affecting the service life of the instrument, so as to prevent torsional movement
- Summary
- Abstract
- Description
- Claims
- Application Information
AI Technical Summary
Benefits of technology
Problems solved by technology
Method used
Image
Examples
embodiment 600
[0025] Embodiments of the present systems and methods provide a strong structure for mounting instrument components. However, in accordance with embodiments of the present systems and methods members may be doubled, as shown in FIG. 6, tripled, or likewise combined, to support heavy parts mounted thereto. Two-member-truss embodiment 600 may be constructed from cord members 601 and 602, joined by spanning strut-tie members 603-606 and secured by screws 607. Components of an instrument may be secured to or on such a truss, such as by using fasteners and stand offs, or in other manners discussed herein or as known in the art, for deployment in the instrument.
[0026] Frames built using the present members may be used to mount components and circuit boards and these frames may in turn be mounted in a chassis, such as a housing or casing, which may in turn be covered or deployed as a part of a rack system or the like. In accordance with embodiments of the present systems and methods, PCBs ...
embodiment 700
[0030] In accordance with embodiments of the present systems and methods members may be deployed for use as a card guide. FIG. 7 is a perspective view of embodiment 700 using embodiments of members 701 and 702 of the present systems to act as a PCB or card guide. Illustrated card guide 700 is comprised of a pair of spaced apart members 701 and 702 disposed in relation to a card location in an instrument, spaced apart a distance appropriate to receive edges of card 703 and support the card in a deployed configuration in the instrument, for example, in a card slot of another PCB, such as a processor board, of the instrument.
[0031] In accordance with embodiments of the present systems and methods members may be deployed in a hinged swing assembly configuration. FIG. 8 is a perspective view of an embodiment using embodiments of the members of the present systems to act as hinged circuit board mounting structure 800. Members 801-815 are shown interconnected in an arrangement to support a...
embodiment 1000
[0035] A beam member framework may be assembled outside of an instrument housing and components mounted to this framework, which may them be anchored in the instrument housing. Alternatively, the beam member framework may be built within the housing and then the components mounted to the framework. Embodiment 1000 of the present methods illustrated in the flow chart of FIG. 10 might be used to deploy embodiments of the present systems, such as illustrated in FIG. 9. At 1001 first beam members to be disposed in the instrument housing structure, such as members 905 and 906 of FIG. 9, may be interlocked with second beam members to be disposed in the instrument housing, such as beam members 902, 903 and 913 of FIG. 9, to provide a framework. The members may be interlocked at 1001 by keying an end (key 106) of a first beam member with a channel (104) defined by a second beam member at 1002; receiving a fastener through a cross-hole (101) of the second member into an end orifice (107) of ...
PUM
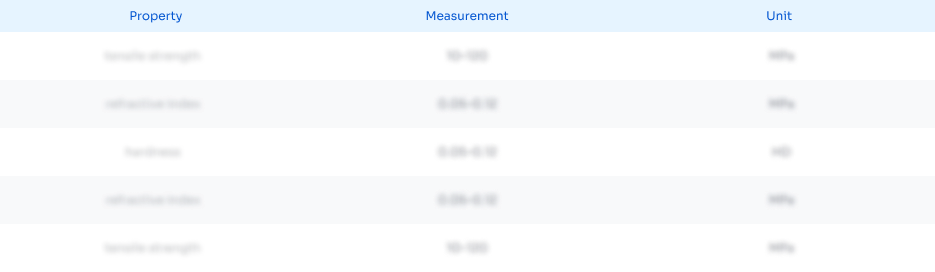
Abstract
Description
Claims
Application Information

- R&D
- Intellectual Property
- Life Sciences
- Materials
- Tech Scout
- Unparalleled Data Quality
- Higher Quality Content
- 60% Fewer Hallucinations
Browse by: Latest US Patents, China's latest patents, Technical Efficacy Thesaurus, Application Domain, Technology Topic, Popular Technical Reports.
© 2025 PatSnap. All rights reserved.Legal|Privacy policy|Modern Slavery Act Transparency Statement|Sitemap|About US| Contact US: help@patsnap.com