Waveguide structures and methods
a waveguide and structure technology, applied in the field of waveguides, can solve the problems of increasing the crosstalk between adjacent communication channels, adverse effects, and rate errors
- Summary
- Abstract
- Description
- Claims
- Application Information
AI Technical Summary
Benefits of technology
Problems solved by technology
Method used
Image
Examples
Embodiment Construction
[0016] According to various exemplary embodiments of systems and methods illustrated herein, a polarization insensitive design space for waveguides and arrayed waveguide grating systems and can be used in, for example, silicon-on-insulator (SOI) micro electromechanical system (MEMS) technology to compensate and to minimize bit rate errors and crosstalk. This polarization insensitive waveguide structure is the basic building block of many components such as an AWG and a switch. These components are the building blocks of many optical network components such as routers and optical add / drop multiplexers that are used by many wavelength division multiplexing (WDM) and dense wavelength division multiplexing (DWDM) technologies. The base geometry can be T-shaped in cross-section, as shown in FIG. 1, and has optimum width and height parameter ranges. By optimizing the ratio between the width and height of the waveguide and the height of base, the TE-TM wavelength shift is minimized to with...
PUM
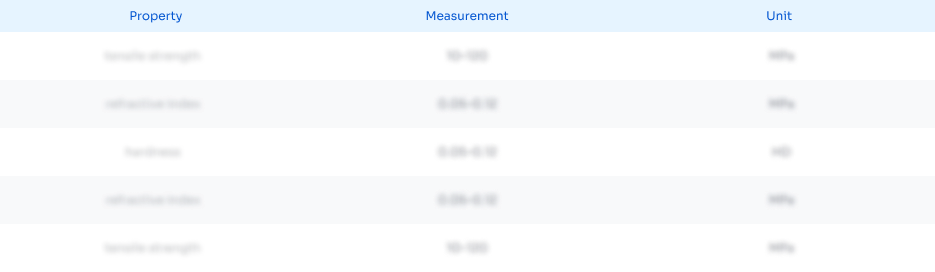
Abstract
Description
Claims
Application Information

- R&D
- Intellectual Property
- Life Sciences
- Materials
- Tech Scout
- Unparalleled Data Quality
- Higher Quality Content
- 60% Fewer Hallucinations
Browse by: Latest US Patents, China's latest patents, Technical Efficacy Thesaurus, Application Domain, Technology Topic, Popular Technical Reports.
© 2025 PatSnap. All rights reserved.Legal|Privacy policy|Modern Slavery Act Transparency Statement|Sitemap|About US| Contact US: help@patsnap.com