Socket for testing a semiconductor device and a connecting sheet used for the same
a technology for semiconductor devices and sockets, which is applied in the field of sockets for testing semiconductor devices and the connection sheets used for the same. it can solve the problems of inability to test semiconductor devices, inability to arrange the probes b>1/b> of the conventional test socket, and inability to demonstrate the function of the socket, so as to achieve sufficient electric contact stably and continuously
- Summary
- Abstract
- Description
- Claims
- Application Information
AI Technical Summary
Benefits of technology
Problems solved by technology
Method used
Image
Examples
embodiment 1
[0064]FIG. 1 is a perspective view illustrating a structure of a test socket according to Embodiment 1 of the present invention. In the figure, numerical reference 1 designates a probe; numerical reference 2 designates a connecting sheet; numerical reference 201 designates a connecting hole; numerical reference 202 designates an electrode pad; numerical reference 100 designates a plunger; numerical reference 101 designates a cylinder; numerical reference 102 designates a coil spring; numerical reference 103 designates a terminal portion, connected to a test board; numerical reference 110 designates a socket base; numerical reference 110a designates a socket lid; numerical reference 110b designates an aligning pin; numerical reference 14 designates a semiconductor package; numerical reference 14a designates an outer connecting terminal; and numerical reference 15 designates a socket.
[0065] In this test socket, an elastically deformative insulating member is used as a base, and the c...
embodiment 2
[0071]FIG. 2 is a cross-sectional view illustrating a structure of a test socket according to Embodiment 2 of the present invention. In the figure, numerical reference 1 designates a probe; numerical reference 2 designates a connecting sheet; numerical reference 201 designates a connecting hole; numerical references 202a and 202b designate electrode pads; numerical reference 203 designates a connecting wire; numerical reference 100 designates a plunger; numerical reference 101 designates a cylinder; numerical reference 102 designates a coil spring; numerical reference 103 designates a terminal portion; numerical reference 110 designates a socket base; numerical reference 110a designates a socket lid; numerical reference 14 designates a semiconductor package; numerical reference 14a designates an outer connecting terminal; numerical reference 15 designates a socket; numerical reference 16 designates a circuit board; and numerical reference 17 designates a connecting pin.
[0072] The c...
embodiment 3
[0074]FIG. 3 is a cross-sectional view illustrating a structure of a test socket according to Embodiment 3 of the present invention. In the figure, numerical reference 1 designates a probe; numerical reference 2 designates a connecting sheet; numerical reference 201 designates a connecting hole; numerical references 202a and 202b designate electrode pads; numerical reference 203 designates a connecting wire; numerical reference 204 designates a protrusion-like electrode; numerical reference 100 designates a plunger; numerical reference 100b designates a slit; numerical reference 101 designates a cylinder; numerical reference 102 designates a coil spring; numerical reference 103 designates a terminal portion; numerical reference 110 designates a socket base; numerical reference 110a designates a socket lid; numerical reference 14 designates a semiconductor package; numerical reference 14a designates an outer connecting terminal; numerical reference 15 designates a socket; numerical r...
PUM
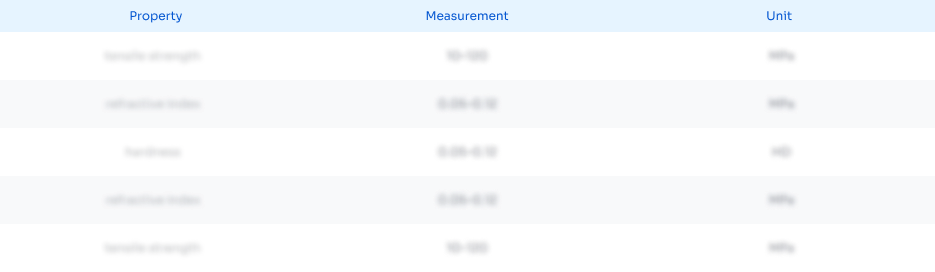
Abstract
Description
Claims
Application Information

- R&D
- Intellectual Property
- Life Sciences
- Materials
- Tech Scout
- Unparalleled Data Quality
- Higher Quality Content
- 60% Fewer Hallucinations
Browse by: Latest US Patents, China's latest patents, Technical Efficacy Thesaurus, Application Domain, Technology Topic, Popular Technical Reports.
© 2025 PatSnap. All rights reserved.Legal|Privacy policy|Modern Slavery Act Transparency Statement|Sitemap|About US| Contact US: help@patsnap.com