Motor Driven Hybrid Rotary Steerable System
a hybrid and rotary steerable technology, applied in the direction of drilling casings, drilling pipes, directional drilling, etc., can solve the problems of mechanical fatigue in the drill pipe, the system using drill bits with little or no side cutting ability may still achieve limited steering response, and the amount of electrical power is reduced. , the effect of great flexibility in implementation
- Summary
- Abstract
- Description
- Claims
- Application Information
AI Technical Summary
Benefits of technology
Problems solved by technology
Method used
Image
Examples
Embodiment Construction
[0017] Referring now to Figures 1-5, when drilling directional boreholes 4 into earthen formations 6, it is common practice to use a bottom hole assembly as shown in Figure 1. The bottom hole assembly (BHA), generally indicated as 10, is typically connected to the end of the tubular drill string 12 which is typically rotatably driven by a drilling rig 14 from the surface. In addition to providing at least a portion of the motive force for rotating the drill string 12, the drilling rig 14 also supplies a drilling fluid 8, under pressure, through the tubular drill string 12 to the bottom hole assembly 10. The drilling fluid 8 is typically laden with abrasive material, as it is repeatedly re-circulated through the borehole 4. In order to achieve directional control while drilling, components of the bottom hole assembly 10 may include one or more drill collars 16, one or more drill collar stabilizers 18 and a rotary steerable system 20. The rotary steerable system 20 is the lowest compo...
PUM
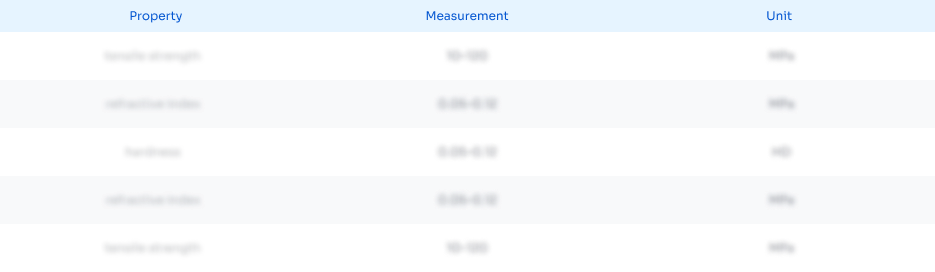
Abstract
Description
Claims
Application Information

- R&D
- Intellectual Property
- Life Sciences
- Materials
- Tech Scout
- Unparalleled Data Quality
- Higher Quality Content
- 60% Fewer Hallucinations
Browse by: Latest US Patents, China's latest patents, Technical Efficacy Thesaurus, Application Domain, Technology Topic, Popular Technical Reports.
© 2025 PatSnap. All rights reserved.Legal|Privacy policy|Modern Slavery Act Transparency Statement|Sitemap|About US| Contact US: help@patsnap.com