Adjustable rotation radius articulated joint for gym machines and knee tutors
a tutoring and adjustable technology, applied in the field of adjustable rotation radius articulated joints for gym machines and knee tutors, can solve the problems of complex knee articular mechanics, anomalous tension, compressive force, etc., and achieve the effect of avoiding the above-mentioned anomalous tension
- Summary
- Abstract
- Description
- Claims
- Application Information
AI Technical Summary
Benefits of technology
Problems solved by technology
Method used
Image
Examples
Embodiment Construction
[0147] More precisely, in a first, simplified configuration applied to a leg extension weight-lifting machine with a resistance (P) constrained to mobile arm L, the articulated joint is formed by two plates 1 and 2; plate 1 is fastened to the weight-lifting machine by means of a bar 1.1, while plate 2 is able to rotate onto plate 1 with reference to a horizontal axis which passes through the femoral condyles of the subject when seated. An arm 2.1, featuring a horizontal rod located at the farther end and connected to the weights, is fastened to plate 2.
[0148] Plate 2 features two openings 2.2 and 2.3 at a right angle to the rotation surfaces of the two plates. The first opening 2.2 is rectangular in shape and the shorter sides are rounded; this opening is made by extending an ideal hole 2.4, which is located at the centre of plate 2, towards the outside along a radius defined as "a" which constitutes the longitudinal axis of symmetry of mobile arm 2.1.
[0149] The ends of the second o...
PUM
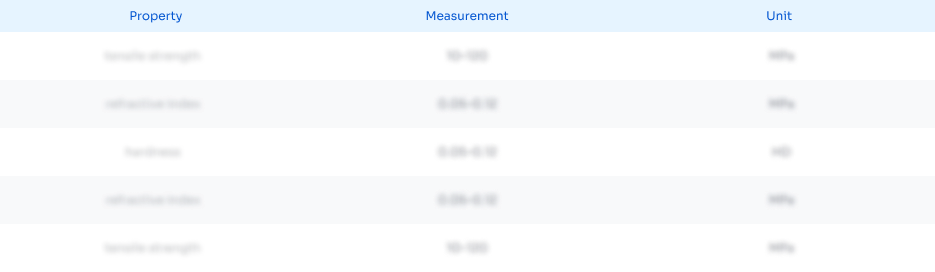
Abstract
Description
Claims
Application Information

- R&D
- Intellectual Property
- Life Sciences
- Materials
- Tech Scout
- Unparalleled Data Quality
- Higher Quality Content
- 60% Fewer Hallucinations
Browse by: Latest US Patents, China's latest patents, Technical Efficacy Thesaurus, Application Domain, Technology Topic, Popular Technical Reports.
© 2025 PatSnap. All rights reserved.Legal|Privacy policy|Modern Slavery Act Transparency Statement|Sitemap|About US| Contact US: help@patsnap.com