Photovoltaic element and method for manufacture thereof
a photovoltaic element and photovoltaic technology, applied in the direction of pv power plants, solid-state devices, semiconductor devices, etc., can solve the problems of reducing conversion efficiency, degrading the characteristic of heterojunction interfaces, and increasing doping, so as to eliminate the lowering of open circuit voltage and short circuit, and improve the output characteristic of photovoltaic elements.
- Summary
- Abstract
- Description
- Claims
- Application Information
AI Technical Summary
Benefits of technology
Problems solved by technology
Method used
Image
Examples
second embodiment
[0084] FIG. 4 is a cross sectional view illustrating the present invention. In this embodiment, a BSF (Back Surface Field) type photovoltaic element in which an internal electric field is introduced on the back surface of the substrate 1 to prevent an effect from the recombination of carriers near the back surface of the substrate 1. An n-type high doping layer 7 is formed on the back surface of the n-type substrate 1 as in FIG. 4.
[0085] The photovoltaic element in FIG. 4 can be formed by the following processes for example. An n-type crystalline silicon substrate 1 which is sliced along (100) surface and of which resistivity is 0.1-10 .OMEGA.cm and of which thickness is 200-400 .mu.m is prepared. As a first process, the substrate 1 is dipped into a 5 wt. % aqueous solution of sodium hydroxide (NaOH) about 85.degree. C. for ten minutes to remove deformation on the surface of the substrate 1. As a second process, the substrate 1 is dipped into a mixed solution containing 1.5 wt. % aq...
third embodiment
[0095] As shown in FIG. 6 of the third embodiment, an intrinsic amorphous silicon layer 2 and a p-type amorphous silicon layer 3 are formed on the front surface of the substrate 1 having uneven sections by a plasma CVD method. A front electrode 4 containing ITO of 1000 .ANG. in thick is formed by sputtering on the p-type amorphous silicon layer 3. A comb-like collecting electrode 5 containing silver is formed by screen printing using Ag paste on the front electrode 4. A back electrode 6 of about 20-25 .mu.m in thick is formed on the back surface of the substrate 1 by using Al paste.
[0096] It is convenient to form a back electrode 6 on the whole back surface of the substrate 1 by screen printing using Al paste from the viewpoint of mass production. In this method, a back electrode 6 containing Al of about 20 .mu.m in thick is formed by pasting Al paste on the whole back surface of the substrate 1 by screen printing and calcinating the paste by approximately 700.degree. C. heat treatm...
fifth embodiment
[0100] FIG. 8 of the fifth embodiment illustrates a BSF-type photovoltaic element manufactured in a low-temperature process without using thermal diffusion. An intrinsic amorphous silicon layer 10 of 50-100 .ANG. in thick is deposited on the back surface of the substrate 1 by a plasma CVD method of low-temperature process using silane (SiH.sub.4) where the temperature of the substrate is about 170.degree. C. A high doping n-type amorphous silicon layer 11 of 50-500 .ANG. in thick is deposited on the intrinsic amorphous silicon layer 10 by using silane (SiH.sub.4) and phospine (PH.sub.3)as a dopant gas. A transparent electrode on a back surface 12 containing ITO of 1000 .ANG. in thick is formed by sputtering. A comb-like collecting electrode 9 is formed on the transparent electrode on a back surface 12 by using Ag paste. By these processes, a substantially intrinsic amorphous silicon is interposed between the crystalline silicon substrate and the amorphous silicon layer on the back s...
PUM
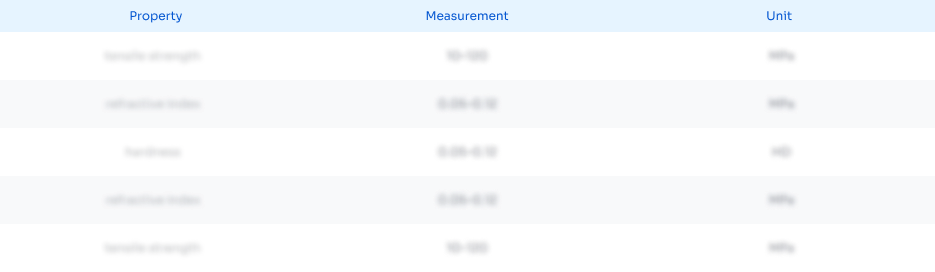
Abstract
Description
Claims
Application Information

- R&D
- Intellectual Property
- Life Sciences
- Materials
- Tech Scout
- Unparalleled Data Quality
- Higher Quality Content
- 60% Fewer Hallucinations
Browse by: Latest US Patents, China's latest patents, Technical Efficacy Thesaurus, Application Domain, Technology Topic, Popular Technical Reports.
© 2025 PatSnap. All rights reserved.Legal|Privacy policy|Modern Slavery Act Transparency Statement|Sitemap|About US| Contact US: help@patsnap.com