Production of MDI-polyurethane microporous elastomer
A technology of microcellular elastomer and polyurethane, which is applied in the field of polyurethane microcellular elastomer preparation, can solve the problems of large dynamic fatigue deformation value of MDI-based microcellular elastomer products, and achieve optimization of physical and mechanical properties and improvement of dynamic fatigue deformation value , the effect of reducing randomness
- Summary
- Abstract
- Description
- Claims
- Application Information
AI Technical Summary
Problems solved by technology
Method used
Image
Examples
Embodiment 1
[0026] Polytetrahydrofuran copolyether with a molecular weight of 2000 reacts with MDI at 70-90°C to obtain a prepolymer with a -NCO content of 6.2%. The chain extender component is mainly 1.4-butanediol, and the foaming agent, catalyst and surfactant account for 3% of the total;
[0027] Using a low-pressure foaming machine, mix the prepolymer and chain extender components according to the ratio of the isocyanate index to 100%, inject the reaction material liquid into a mold at 90°C to manufacture a microcellular elastomer test piece, and demould after 15 minutes. After aging at 110° C. for 15 hours.
[0028] The tested static mechanical properties are the same as in Comparative Example 1.
[0029] The measured dynamic fatigue performance is the same as that of Comparative Example 1.
[0030] The test results are shown in Table 1.
Embodiment 2
[0032] Polycaprolactone with a molecular weight of 2000 reacts with MDI at 70-90°C to obtain a prepolymer with an -NCO content of 7.8%. The chain extender component is mainly 1.4-butanediol, and the foaming agent, catalyst, and surfactant account for 5% of the total; a low-pressure foaming machine is used to mix the prepolymer and For the chain extender component, inject the reaction liquid into a mold at 90°C to make a microporous elastomer test piece, demould it after 15 minutes, and post-cure at 110°C for 15 hours.
[0033] The tested static mechanical properties are the same as in Comparative Example 1.
[0034] The measured dynamic fatigue performance is the same as that of Comparative Example 1.
[0035] The test results are shown in Table 1.
Embodiment 3
[0037] Polycaprolactone with a molecular weight of 2500 reacts with MDI at 70-90°C to obtain a prepolymer with an -NCO content of 9.5%. The chain extender component is mainly 1.4-butanediol, and the foaming agent and catalyst surfactant account for 8% of the total; a low-pressure foaming machine is used to mix the prepolymer and extender according to the ratio of isocyanate index to 100%. For the chain agent component, inject the reaction material liquid into a mold at 90°C to make a microporous elastomer test piece, demould after 15 minutes, and post-cure at 110°C for 15 hours.
[0038] The tested static mechanical properties are the same as in Comparative Example 1.
[0039] The measured dynamic fatigue performance is the same as that of Comparative Example 1.
[0040] The test results are shown in Table 1.
[0041] Table 1: Static and dynamic mechanical properties of the microcellular elastomers prepared in comparative example 1 and examples 1-3
[0042] serial ...
PUM
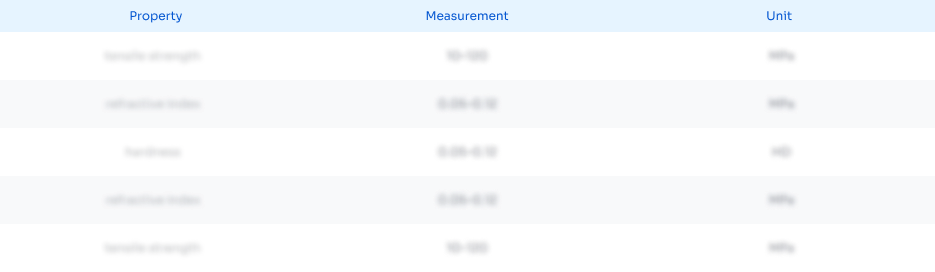
Abstract
Description
Claims
Application Information

- R&D Engineer
- R&D Manager
- IP Professional
- Industry Leading Data Capabilities
- Powerful AI technology
- Patent DNA Extraction
Browse by: Latest US Patents, China's latest patents, Technical Efficacy Thesaurus, Application Domain, Technology Topic, Popular Technical Reports.
© 2024 PatSnap. All rights reserved.Legal|Privacy policy|Modern Slavery Act Transparency Statement|Sitemap|About US| Contact US: help@patsnap.com