Wound coil type inductor
A wire-wound inductor and wire-wound part technology, applied in the direction of inductors, fixed inductors, sensors, etc., can solve the problems of different multiple resonance frequencies, single, etc., and achieve the effect of cost reduction
- Summary
- Abstract
- Description
- Claims
- Application Information
AI Technical Summary
Problems solved by technology
Method used
Image
Examples
Embodiment 1
[0071] A specific embodiment 1 of the present invention will be described with reference to the drawings.
[0072] This embodiment is a wire-wound inductor formed by winding a wire 2 on a magnetic core 3 . In addition, the magnetic core 3 can be made of ferrite or dielectric, and it can also be a magnetic core composed of a mixture of resin and iron powder filled in an air-core coil. As such a wire-wound inductor, a commonly used magnetic core is used. 3. The structure of ferrite is adopted in this embodiment. In addition, a copper wire is used for the wire 2 .
[0073] The magnetic core 3 has a shape having a pointed portion 11 whose outer diameter gradually decreases so that the winding diameter of the above-mentioned wire 2 wound on the magnetic core 3 is not constant but gradually becomes smaller.
[0074]The pointed part 11 formed on this magnetic core 3 is that the outer diameter of the above-mentioned magnetic core 3 is not tapered from the large-diameter base end of ...
Embodiment 2
[0095] A specific embodiment 2 of the present invention will be described with reference to the drawings.
[0096] This embodiment is another example of the above-mentioned embodiment 1. Specifically, as shown in FIG. 6 , a pointed-shaped magnetic core 3 is housed in a case 4 to form a wire-wound inductor.
[0097] Specifically, the above-mentioned magnetic core 3 has a structure in which a non-winding portion 3B on which the above-mentioned wire 2 is not wound is integrally provided on an end portion of the winding portion 3A around which the above-mentioned wire 2 is wound, and by fixing the non-winding portion 3B The case 4 has a structure in which the winding portion 3A of the magnetic core 3 is accommodated in a non-contact state with respect to the case 4 . The connecting terminal portion 5 connected to the circuit wiring of the above-mentioned substrate 1 is provided on the non-winding portion 3B of the above-mentioned magnetic core 3 or the above-mentioned case 4, ther...
Embodiment 3
[0117] A specific embodiment 3 of the present invention will be described with reference to the drawings.
[0118] This embodiment is another example of the above-mentioned embodiment 2. Specifically, as shown in FIG. The structure is as follows: on the outer peripheral surface of the non-winding portion 3B of the magnetic core 3 where the above-mentioned wire 2 is not wound, a reflective member 7 having a higher electromagnetic wave reflection characteristic than the magnetic core 3 is provided along the circumference, and the reflective member 7 is combined with the magnetic core 3. The wire 2 wound on the magnetic core 3 is set in a connected state.
[0119] Therefore, in addition to the attenuation characteristics exhibited by the winding portion 3A of the above-mentioned magnetic core 3, the above-mentioned reflective member 7 also exhibits reflection characteristics, so through the isolation effect of the attenuation characteristics and reflection characteristics, higher...
PUM
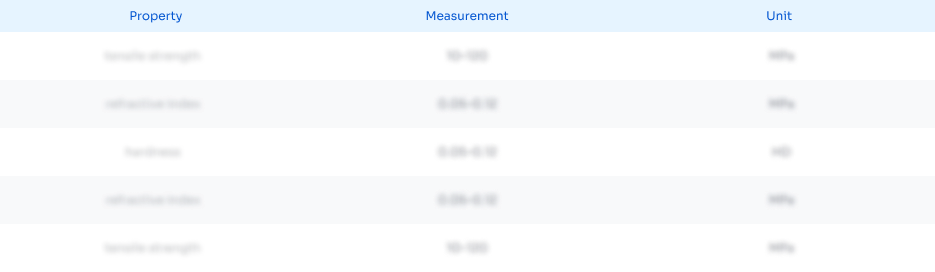
Abstract
Description
Claims
Application Information

- R&D
- Intellectual Property
- Life Sciences
- Materials
- Tech Scout
- Unparalleled Data Quality
- Higher Quality Content
- 60% Fewer Hallucinations
Browse by: Latest US Patents, China's latest patents, Technical Efficacy Thesaurus, Application Domain, Technology Topic, Popular Technical Reports.
© 2025 PatSnap. All rights reserved.Legal|Privacy policy|Modern Slavery Act Transparency Statement|Sitemap|About US| Contact US: help@patsnap.com